[ Instrument R & D of Instrument Network ] In recent years, flexible pressure sensor devices have attracted more and more attention from industry, academia, and research circles due to their wide application in human-computer interaction, electronic skin, and smart wearable fields. However, when the traditional flexible sensor device is applied in a real flexible substrate scene, the vertical stress along the normal direction caused by the device bending will produce a "false signal", so how to ensure the reliability and stability of the final device performance is still A very urgent need. In addition, achieving a wider dynamic linear range usually comes at the expense of device sensitivity, and vice versa, how to solve the balance between device sensitivity and dynamic linear range through structural design and material selection is still not a small one challenge. In order to solve the above problems, Chen Ming, associate researcher, Yang Chunlei and his collaborators of the Photonic Information and Energy Materials Research Center of the Institute of Materials Research, Shenzhen Institute of Advanced Technology, Chinese Academy of Sciences proposed two solutions.
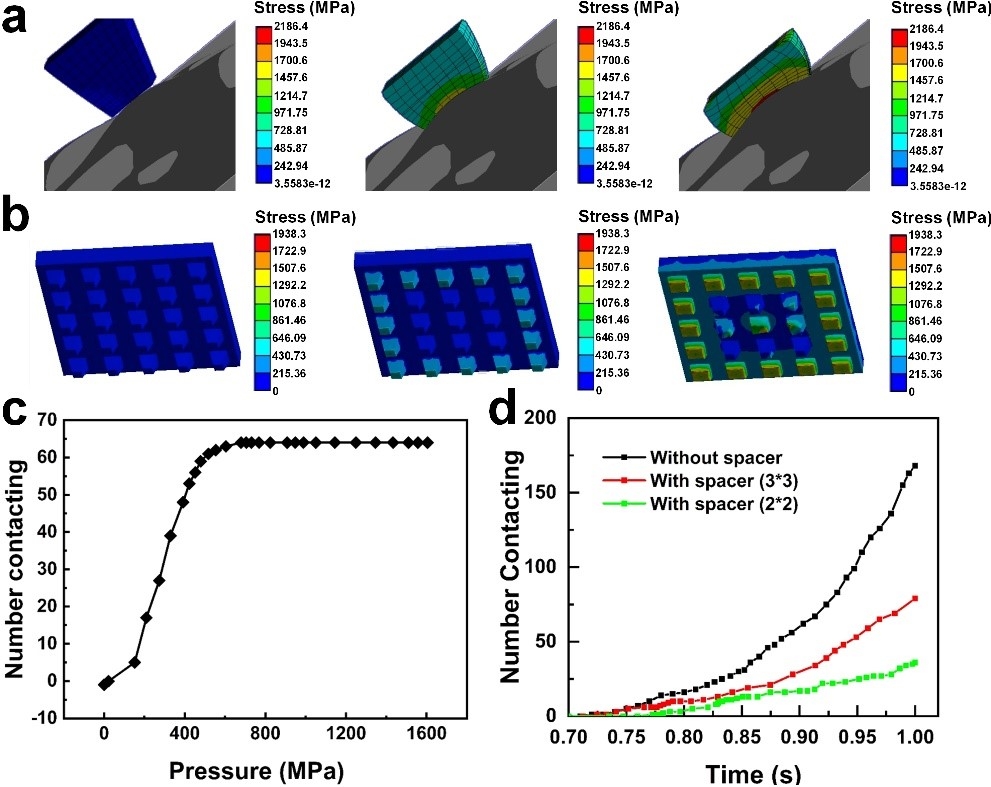
Figure 1 Finite element analysis based on flexible pressure sensor device
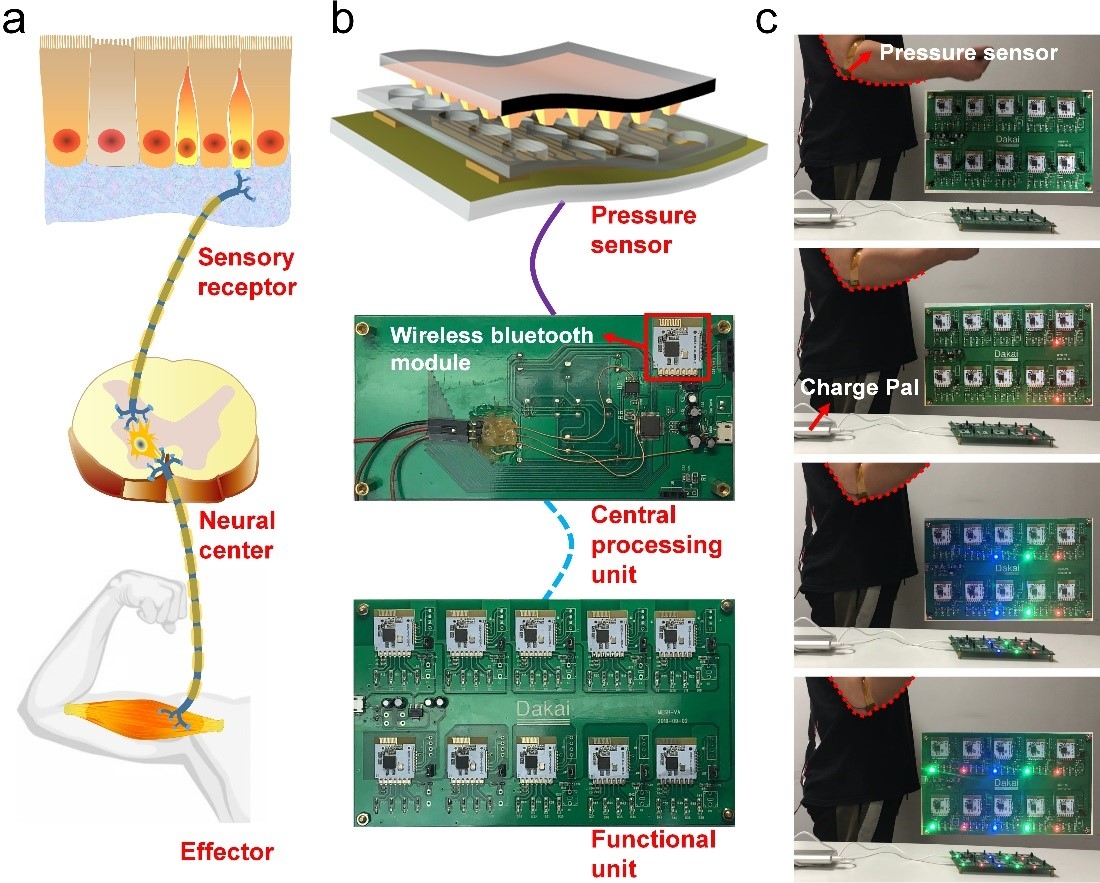
Figure 2 Schematic diagram of the human body and artificial reflection arc, and the physical image of artificial reflection arc in real scene
The researchers used traditional micro-nano processing technology, vacuum coating technology and laser scribing technology to prepare polydimethylsiloxane (PDMS) / aluminum-doped zinc oxide (AZO) with a micro-round table structure on the top, and the spacer layer as a photoresist (PS) and bottom interdigital electrode are flexible pressure sensors with polyimide (PI) / gold (Au). The fabricated device has a sensitivity of up to 2200 kPa-1, a dynamic linear range of up to 9.6 kPa, and excellent performance such as rise and fall response times as fast as less than 20 ms. The researchers further clarified the working mechanism and internal pressure distribution of the device under the action of external pressure from a theoretical perspective, and explained the size of the hole diameter in the PS spacer layer, the microstructure of the conductive layer and the final device sensitivity, the dynamic linear range and the sensitivity threshold, etc. Performance relationship. Recently, the above research results were published in the well-known energy journal Nano Energy (DOI: 10.1016 / j.nanoen.2020.104743, IF =, titled "High-performance zero-standby-power-consumption-under-bending pressure sensors for artificial reflex arc" 15.548).
In addition, the researchers also designed a spacer layer based on polydimethylsiloxane (PDMS) / carbon black (CB), patterned polyimide (PI), and laser-induced graphene (LIG) High-performance interdigital electrode, flexible pressure sensor with zero standby power loss. The prepared flexible pressure sensor has high sensitivity (43 kPa-1), wide linear response range (0.4 ~ 13.6 kPa), fast response (<30 ms), long-term cyclic stability (> 1800 cycles) and in certain bending Under the condition (bending angle: 0 ~ 5 °), it also has the performance of standby zero power loss. The researchers also experimentally and theoretically studied the effect of the diameter of the PI spacer on the performance of the flexible pressure sensor. Related research results were also recently published in the journal ACS Applied Materials & Interfaces (DOI: 10.1021 / acsami.0c02774, IF = "Highly Sensitive and Wide Linear-Response Pressure Sensors Featuring Zero Standby Power Consumption under Bending Conditions" 8.456). The above work was jointly completed by He Ke, a joint graduate student, Yi Chenghan, a joint graduate student, and Hou Yuxin, a formal graduate student.
The above research was supported by projects such as the National Natural Science Foundation of China and the Shenzhen Basic Research Layout Project.
Froling Boiler,Waste Heat Boiler,Crop Waste Boiler,Waste Recovery Boiler
Jinan Boiler Group Co., Ltd. , http://www.jinanboiler.com