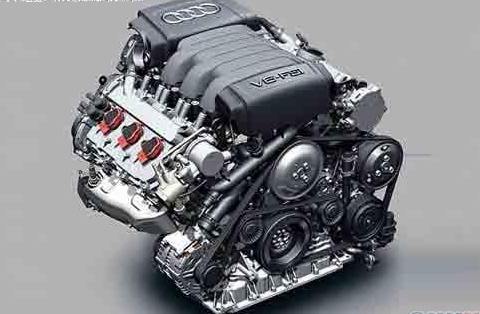
FSI is a VW/Audi gasoline direct injection technology. FSI can directly inject fuel into the combustion chamber, reducing the heat loss of the engine, thereby increasing the output power and reducing the fuel consumption. Both fuel economy and power are helpful. TFSI is a turbocharged (T) FSI engine, abbreviated as TFSI, which is commonly referred to as the Audi series. The Volkswagen series direct injection and turbocharged engine is abbreviated as TSI. However, due to the problem of domestic oil products, the domestic Audi TFSI did not use stratified combustion technology. Below, we will explain the Audi TFSI and FSI technologies separately.
The new 3.0 TFSI: the high-tech V6 supercharged engine <br> <br> strong power and torque output linear growth, high efficiency, and this is the top version of Audi's V6 engine range. The 3.0 TFSI engine is capable of delivering 213 kW (290 hp) of maximum power and 420 N•m of powerful torque, enabling a combination of two cutting-edge technologies – gasoline direct injection and supercharging.
The Audi brand, marked by the Fourth Ring, has a long tradition of using super-powered engines. Audi's predecessor Auto Union was already equipped with a supercharger in the European GP Grand Prix racing car produced in the 1930s, which gave a powerful 440-kilowatt output for a 16-cylinder and 12-cylinder engine. Horse power. After the end of the 1970s, Audi began focusing on turbocharger technology, which helped Audi dominate the world of motor sports. That is, since then, Audi turbocharged engines began to succeed in the market, causing a huge stir.
The supercharger is now making a comeback, providing the ideal supercharger technology for the new 3-litre V6 TFSI engine. The letter "T" in the Audi engine series no longer represents only turbocharging, but instead represents the forced intake of the engine. The supercharger has a compact design and can be easily “squeezed†into the original intake manifold position within the 90° V-cylinder group. Thanks to the multi-wedge belt drive, powerful traction can be provided at idle start of the engine. The 3.0 TFSI engine also achieves a peak torque of 420 N•m at a low speed of 2500 rpm and can continue to 4850 rpm.
The gas path of the supercharger is very short, which means that the torque increases very quickly, and the response speed even exceeds that of a naturally aspirated engine with the same amount of exhaust gas. The 3.0 TFSI engine is very responsive to the throttle and can be easily lifted to 6500 rpm and at 4850 rpm it can reach a rated output of 213 kW (290 bhp).
The highest fuel efficiency 3.0 TFSI engine fully deserves the highest fuel efficiency score. Its powerful traction can be used with a wider range of gearbox transmission ratios to further improve its already outstanding fuel efficiency. In fact, this 3.0 TFSI engine is installed on any longitudinal engine Audi model, and its average fuel consumption will not exceed 10 liters/hundred kilometers. The exhaust emissions of this engine have reached the unimplemented Euro 5 standard - this represents Audi's latest engine standard.
The Audi gasoline direct injection technology that complies with the FSI principle is the first prerequisite for achieving industry-leading fuel efficiency. Unlike traditional concepts, the use of FSI technology allows the supercharger to be placed behind a throttle valve. In this way, the density of air passing through the supercharger under low load or circulation conditions is very low, and the rotor is almost free to rotate, so that the required driving force is negligible. The engine's compression ratio of up to 10.5:1 also plays a significant role in improving efficiency. The same is true for the use of FSI's direct fuel injection technology. The violently rotating fuel vortex quickly cools the combustion chamber, reducing the probability of engine knock.
The supercharger used in the new 3.0 TFSI engine has two four-lobe rotating pistons in the supercharger at speeds of up to 23,000 rpm, and the blade-to-shell clearance is only a few thousandths of a millimeter. The rotor can deliver 1000 kg of air per hour.
The two aluminum water-cooled intercoolers that are integrated are each connected to a separate cooling circuit through which the compressed hot air is cooled again, increasing the oxygen content of the air entering the combustion chamber. This series of measures minimizes the supercharger noise.
The new engine itself belongs to Audi's epoch-making V-engine series. In addition to having a standard 90-degree angle cylinder, one of its characteristics is the lightweight construction - the aluminum-silicon cast 3 liters displacement crankcase weighs only 33 kilograms. The engine, including the supercharger, weighs only 189 kilograms; the bore diameter is 84.5 millimeters, the stroke is 89 millimeters, and the displacement is 2995 cubic centimeters.
Enhanced crankcase <br><br> Audi has adopted a series of high technology on the 3.0 TFSI engine. Increased stress levels in the crankcase reduce frictional resistance between related components. Two intake camshafts have a phase adjustment range of 42 crankshafts. As a result, an intake vortex that is more conducive to the mixture of oil and gas is formed in the intake passage.
The injection fuel system is a completely new design. The six-hole fuel injection nozzle of the common-rail injection system injects fuel directly into the combustion chamber at a high pressure of 150 bar. The fuel nozzle's superior response allows it to inject up to 3 fuel injections per compression stroke to optimize the combustion process and further enhance the performance of the new 3.0 TFSI.
FSI: fuel injection technology <br> <br> energy constantly scarce today, who let the engine while reducing energy consumption and more power play, the future will be won by a bigger market.
FSI is the abbreviation of Fuel Stratified Injection. It means that fuel stratified injection is an innovative and revolutionary technology in the field of direct injection gasoline engines. The FSI® direct injection technology used by Audi achieves the perfect combination of engine power and fuel economy at the same displacement. It is the most mature and advanced direct fuel injection technology in the engine technology of today's automotive industry and leads the way in gasoline engines. The development trend.
The FSI engine that injects fuel directly into the cylinder has advantages over traditional engines that inject fuel into the intake manifold: a significant increase in power; higher torque and power output; and a 15% reduction in fuel consumption.
When the driver is driving on the road, the deepest experience is the reduced number of shifts, easier handling, and fuel savings. Compared with conventional engines, a 15% reduction in fuel consumption means that the engine's economy has increased by 15%, which is a comprehensive result of the continuous improvement of FSI's technologies. For the public environment, this technology has laid a good foundation for the reduction of automobile exhaust emissions in the future.
In addition, FSI® gasoline direct injection engines using FSI's direct fuel injection technology are superior in power. It has demonstrated extraordinary potential in the world's most severe durability test. The Audi R8 equipped with this engine has repeatedly won the Le Mans competition and won numerous championships in the ALMS American Le Mans Series.
Exhaust emission control <br> <br> complex exhaust gas purification system based on two catalytic converters, it is one of the characteristics of FSI technology.
<br> <br> storage converter in an engine exhaust end is attached to an important component of effective control of exhaust emissions, i.e., exhaust gas recirculation system. The new system is more efficient than its predecessor and can re-circulate 30% of the exhaust gas to the engine's combustion chamber.
Two catalytic converters are also installed on the engine to control emissions: One of the three-stage catalytic converters is located at the exhaust end of the exhaust manifold, ie close to the engine, while the other NOx storage converter is It is located under a dish-shaped floor.
The NOx storage converter is specially designed for direct fuel injection engines and has a NOx sensor on its exhaust side. Traditional three-way catalytic converters cannot fully decompose nitrogen oxides during the lean phase of the engine; therefore, components in the exhaust gas will contain a large amount of harmful chemicals. In order to convert a large amount of residual nitrogen oxides into harmless nitrogen, a storage catalytic converter containing a tantalum metal coating can accomplish this task efficiently.
The storage converter is controlled by the set operating characteristics and temperature. When the converter reaches saturation, the engine generates a more concentrated mixture of gases in a short period of time. This raises the temperature of the exhaust gas, at which point the helium molecules of the converter coating begin to release nitrogen oxides. Nitrogen oxides are then converted to nitrogen. The operating frequency for purifying high-concentration gas mixtures is determined by the operating conditions of the engine. However, on average, within a few minutes of operation, there will be a few seconds to purify the exhaust gas.
With regard to exhaust gas control: After passing through a multi-stage catalytic converter (located downstream of the engine), the exhaust gas passes through a storage type catalytic converter (below a pan-shaped floor) containing a base metal coating. The storage catalytic converter extracts and stores the nitrogen oxides (red) produced in the stratified charge phase from the exhaust gas.
The ruthenium coating of the storage catalyst combines with a high exhaust temperature to convert nitrogen oxides into harmless nitrogen (orange).
<br> <br> uniform pattern in a homogeneous charge mode, the air can be fully opened when the throttle valve into the combustion chamber through the entire cross section of the intake air.
More power and torque In the intake manifold of the FSI engine, the "inflated flap" opens at high engine speeds. Air enters the combustion chamber through the entire section without any hindrance.
As the fuel is directly injected into the combustion chamber as the air flows in, a homogeneous mixture of oil and gas is produced throughout the combustion chamber. With this cooling fuel direct injection (internal cooling), a higher compression ratio can be achieved than with a conventional natural engine. As a result, full and efficient combustion provides more power without increasing fuel consumption and emissions.
Special gear clock including table and Wall Gear Clock. For the Desk Gear Clock, there is alarm and time function gear clock. For the wall gear clock, we have different sizes of wall gear clock, 14 inch small wall gear clock and the 20 inch super large gear clock. You can see the moving of every gear. That's interesting. Like you are seeing the time moving.
Wood Gear Grandfather Clock,Antique Clock Gears Images,Antique Clock Gears For Sale,Clock With Moving Gears
Guangzhou Huan Yu Clocking Technologies Co., Ltd. , https://www.mk-time.com