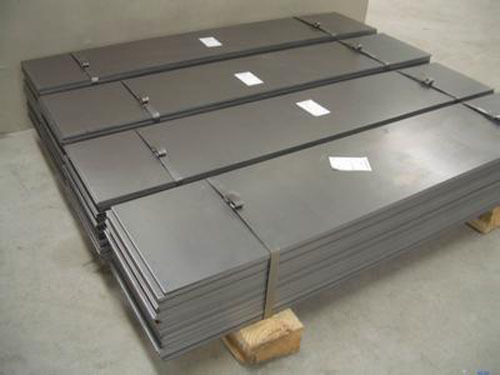
Welded composite billet method
Several patents of JFE have proposed a method of welding two or more continuous casting slabs into a composite slab and then rolling them with a welding method. Under the condition that the compression ratio is less than 2.0, special thick steel plates are produced. Representative patents Chartered public patents. The technical points of this patent are:
1) Production of Composite Slabs: Grinding of the mating surfaces of continuous casting slabs with a belt grinder removes the black surface of the slabs to a thickness of about 2 mm. The slabs are stacked and placed in a vacuum chamber. The air pressure between the interfaces is less than 1Pa, and the entire circumference of the slab is sealed by electron beam welding or inert gas shielded welding.
2) Steel plate rolling: The composite slab is heated (heating temperature is higher than 1000°C), rolled into extra thick steel plate (compression ratio is less than 2.0), and the time t (seconds) after cooling to 500°C after rolling is to satisfy t≥ ( Ra)2/0.15, Ra is the thickness (μm) of the joint surface. The largest specification listed in the patent specification is (308mm + 308mm) slabs rolled into 340mm plates (compression ratio 1.8).
Continuous casting method
The key to Sumitomo Metal's patented technology is to control the center of the billet during continuous casting. That is, the press roll is set at the end of the continuous casting machine. When the solid fraction in the center of the billet is greater than 80%, the billet is subjected to a large press force. Reducing the degree of looseness of the center of the slab can be achieved, so that the reduction ratio at the time of rolling can be reduced. The above slab can be rolled with a reduction ratio of 1.5 to 2.5 using the conventional equipment to obtain an extremely thick steel sheet with excellent internal quality. The 300mm continuous casting slab made by this method can be rolled into 200mm thick steel plate.
This patent studies the relation between the central loose volume (Vp0/cm2.g-1) and the casting reduction (d/mm) of the billet and obtains the relationship of Vp0=10-(a×d+b). Where a and b are constants related to the strength of the steel. Experiments have shown that, by appropriate casting reduction d, when Vp0 ≤ 0.9×10-4, the steel plate rolled with a small reduction ratio can adopt an ultrasonic testing method that requires more stringent pressure vessels than can be achieved. Qualified requirements. The patented slab reduction d is 8-30 mm. The patent also shows that the relationship between the central void volume Vp0 of the slab, the central loose volume Vp of the plate product, and the reduction ratio r of the slab is: Vp=Vp0/r.
Rolling method with specified compression ratio and final pass reduction
The published patent provides a method for producing extremely thick steel plates that are only rolled and have a compression ratio of less than 2.0. The patent decomposes the press-bonding of the center of the continuous casting slab into two processes: the loosening of the central hollow interface and the loosening of the center by diffusion. Accordingly, the rolling points proposed by this patent are:
1) The compression ratio r and the final pass reduction (t0-t1) should satisfy the following relation: r ≥ 0.2 × d0 + 1.0 where d0 is the thickness of the central loose zone of the continuous casting slab, which can be obtained from the continuous casting process. The relationship between the conditions and the thickness of the central loose zone can be determined, and it can also be determined by sampling on the continuous casting slab. T0 is the thickness (mm) before the final pass of the rolled material is pressed. T1 is the thickness after the final pass of the rolled material.
2) The rolling pass specified in this patent does not include a few percent of the rolling pass to adjust the shape of the plate, but as long as the conditions specified in the patent are satisfied, adjusting the plate-shaped rolling has no effect on the quality of the steel plate. .
3) In order to improve the performance of the steel plate, the steel plate can be controlled and rolled, controlled cooling, quenched and tempered.
4) Continuous casting slabs with as little center porosity as possible should be used.
The above is a method of producing extra-thick steel sheets from continuous casting bills by summarizing the search and analysis of patents for extra-thick steel sheets in recent years in Japan. It should be pointed out that most of the above patented technologies are directed against a certain technical difficulty. Therefore, when we use these patented technologies to develop special thick plates, we should comprehensively analyze them to achieve better results.
The intrinsic quality of special heavy plates depends to a large extent on the quality of steelmaking and continuous casting. Therefore, there are some new requirements for continuous casting equipment and processes. It is pointed out that vertical type continuous casting machines may produce special thick plates. The use of billets is more advantageous.
An organic modified Silica Sol is composed of silica particles, organic solvent and modifier. The organic modified silica sol contains silica particles of 17 ~ 22% by mass, organic solvent of 63 ~ 82.5% by mass, and modifier of 0.5 ~ 15% by mass.The organic modified silica sol has suitable average particle size, clear and transparent appearance and good stability.In the hardening film coating solution of resin system has excellent dispersion and stability, can eliminate all kinds of related coating defects, and has excellent water and oil repellent performance.
Organic Modified Silica Sol,Organically Modified Silica Sol,Organically Modified Silica,Organically Modified Silica Coating
SHANDONG YINFENG NANO NEW MATERIALS CO., LTD. , https://www.yinfengsilica.com