I. Introduction
Press machines are a series of machines utilized in the sheet metal processing industry with diverse types and functions. The press machine is primarily employed to alter the form and size of metal plates through pressure, resulting in the final workpiece.
In the sheet metal processing industry, a press brake and a punch press are two common processing equipment that play an important role in sheet metal processing. While they both have similar functions and can carry out various processing processes to produce final profiles, each machine has its own set of advantages and disadvantages and operates differently.
In this blog post, we will compare and contrast the differences, advantages, and disadvantages of these two sheet metal manufacturing processes to provide a better understanding. Here is the video about press brake vs punch press, let's start:
II. What Is Press Brake?
1. Concept and Structure
The press brake is a type of machine tool used to bend metal sheets into desired shapes and angles in sheet metal fabrication. The standard configuration of a press brake typically includes a driving device, ram, workbench, die, and punch.
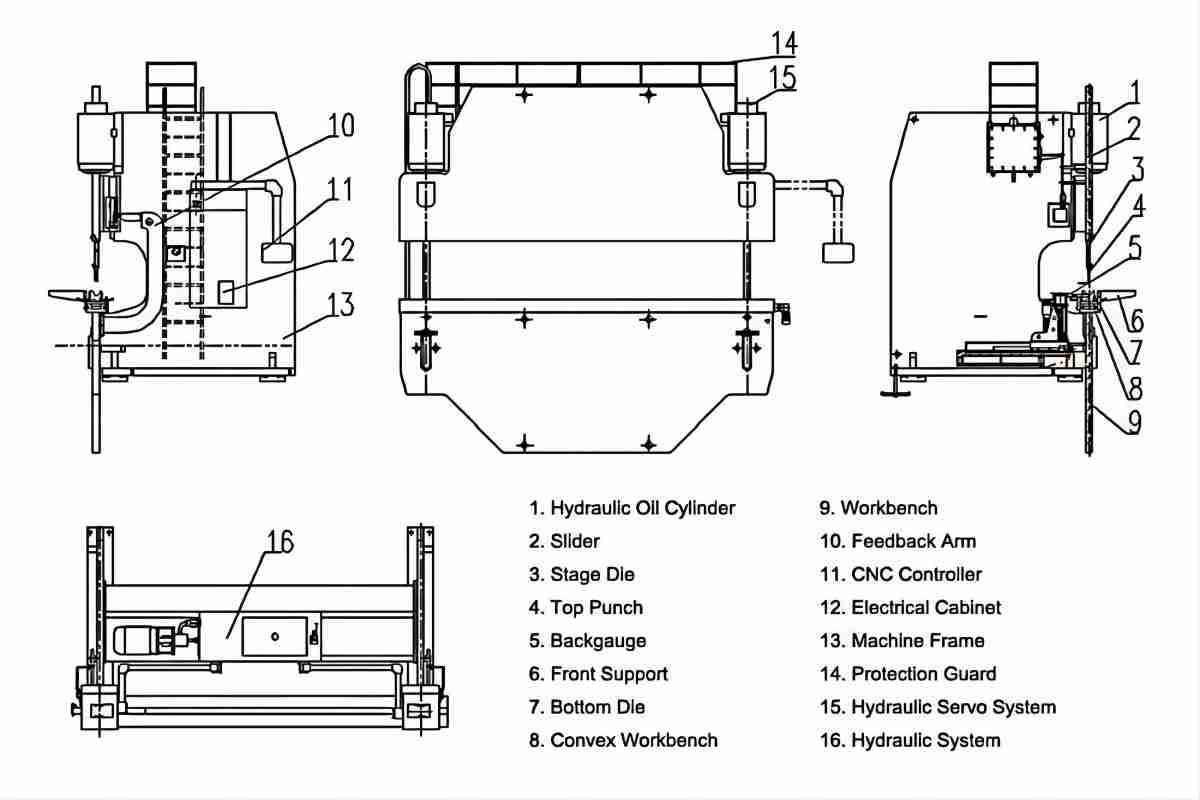
The ram drives the upper die to press down on the metal plate, thereby completing the bending process. The press brake can be adjusted for multiple bends and angle changes, achieved by altering the punch and bottom die sets.
2. Types of press brake
There are various types of press brakes, which can be classified into four categories based on the driving mechanism of the machine: mechanical, pneumatic, hydraulic, and servo-electric.
(1)Mechanical Press Brakes
Working Mechanism:
Mechanical press brakes operate using a flywheel that transforms circular motion into linear motion and stores energy, and releases it through a clutch mechanism to drive the ram. The flywheel is powered by an electric motor, and the clutch engages to transfer the rotational energy to the ram, causing it to move up and down. The mechanical nature of these machines allows for high-speed operation and consistent stroke lengths.
Applications:
Mechanical press brakes are well-suited for high-volume production environments where speed and repeatability are crucial. They are commonly used in the automotive industry for stamping and forming parts, as well as in the production of small to medium-sized components where precision and speed are paramount.
Advantages:
- High-speed operation
- Consistent stroke length
- Suitable for high-volume production
Disadvantages:
- Limited flexibility in stroke adjustment
- Higher maintenance due to mechanical components
(2) Hydraulic Press Brakes
Working Mechanism:
Hydraulic press brakes utilize hydraulic cylinders to move the ram. These cylinders are powered by hydraulic fluid, which is pressurized by a pump. The pressure can be precisely controlled, allowing for adjustable stroke lengths and variable tonnage. This flexibility makes hydraulic press brakes highly versatile.
Applications:
Hydraulic press brakes are ideal for a wide range of applications, from small job shops to large-scale manufacturing. They are particularly useful for bending thicker materials and for applications requiring variable stroke lengths and tonnage. Industries such as aerospace, shipbuilding, and heavy machinery manufacturing often rely on hydraulic press brakes.
Advantages:
- Adjustable stroke length and tonnage
- Capable of bending thicker materials
- Versatile and adaptable to various applications
Disadvantages:
- Slower operation compared to mechanical press brakes
- Higher energy consumption due to hydraulic systems
(3) Servo-Electric Press Brakes
Working Mechanism:
Servo-electric press brakes use electric motors to drive the ram. These motors are controlled by a servo system, which provides precise control over the ram's movement. The absence of hydraulic fluid and mechanical clutches makes servo-electric press brakes cleaner and more energy-efficient.
Applications:
Servo-electric press brakes are ideal for applications requiring high precision and energy efficiency. They are commonly used in the electronics industry, medical device manufacturing, and other sectors where cleanroom conditions are necessary. The precise control offered by servo systems also makes them suitable for intricate bending operations.
Advantages:
- High precision and repeatability
- Energy-efficient and environmentally friendly
- Low maintenance due to fewer mechanical components
Disadvantages:
- Higher initial cost
- Limited tonnage compared to hydraulic press brakes
(4) Pneumatic Press Brakes
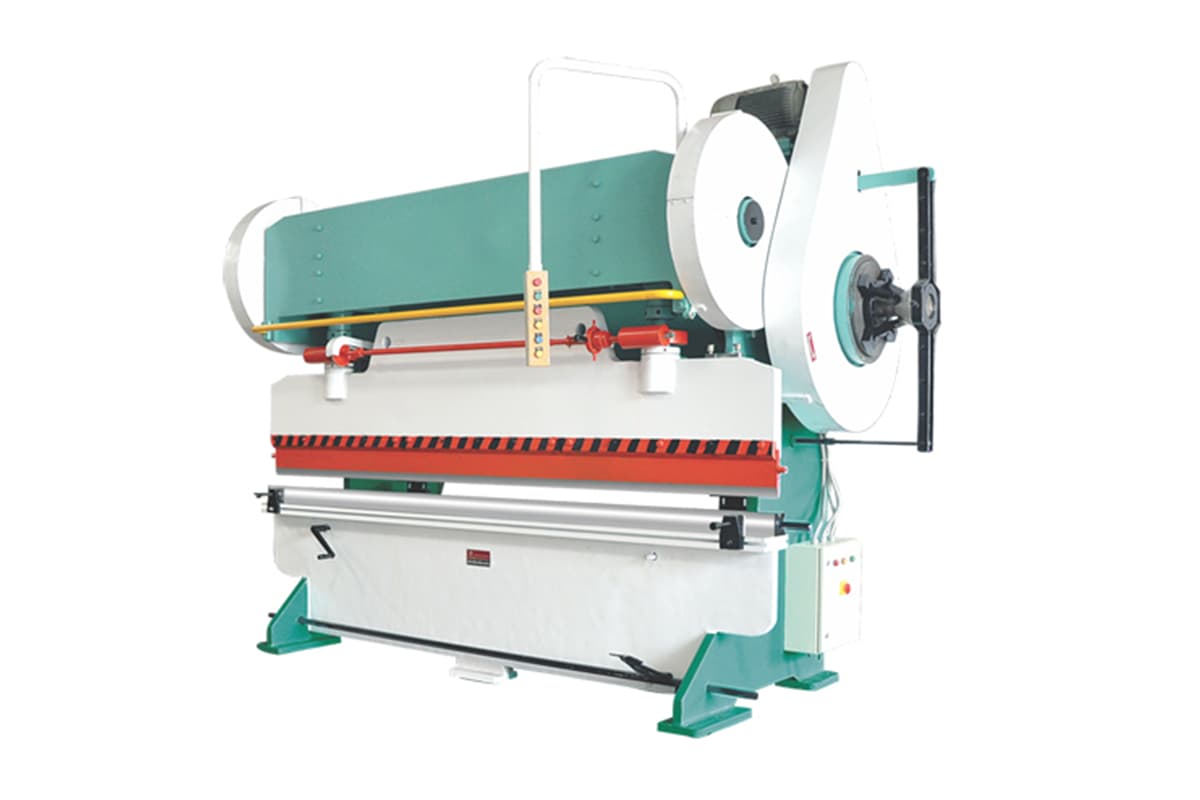
Working Mechanism:
Pneumatic press brakes use compressed air to generate the force needed for bending sheet metal. The compressed air is stored in a tank and directed into air cylinders connected to the ram. The air pressure drives the ram downward, pressing the punch onto the sheet metal positioned on the die, thus bending it into the desired shape. After the bending operation, the air is released, and the ram returns to its initial position.
Applications:
Pneumatic press brakes are suitable for light to medium-duty applications, particularly where high-speed operation is required. They are commonly used in light fabrication for bending thin sheet metals, electronics industry for creating enclosures and brackets, automotive sector for producing small components, HVAC systems manufacturing, and in the production of parts for household appliances like washing machines and refrigerators.
Advantages:
- High-speed operation compared to hydraulic press brakes
- Low maintenance due to fewer moving parts and no hydraulic fluid
- User-friendly and easy to set up and adjust
- Cost-effective with lower initial costs
- No risk of oil leakage
Disadvantages:
- Limited force generation, unsuitable for bending thicker or harder materials
- Noisy operation may require additional noise control measures
- Lower precision compared to hydraulic or servo-electric press brakes
- Not suitable for heavy-duty applications due to lower tonnage capacity
Pressure applied on the metal plate is measured in tonnage units, with the required tonnage increasing as the thickness of the plate increases.
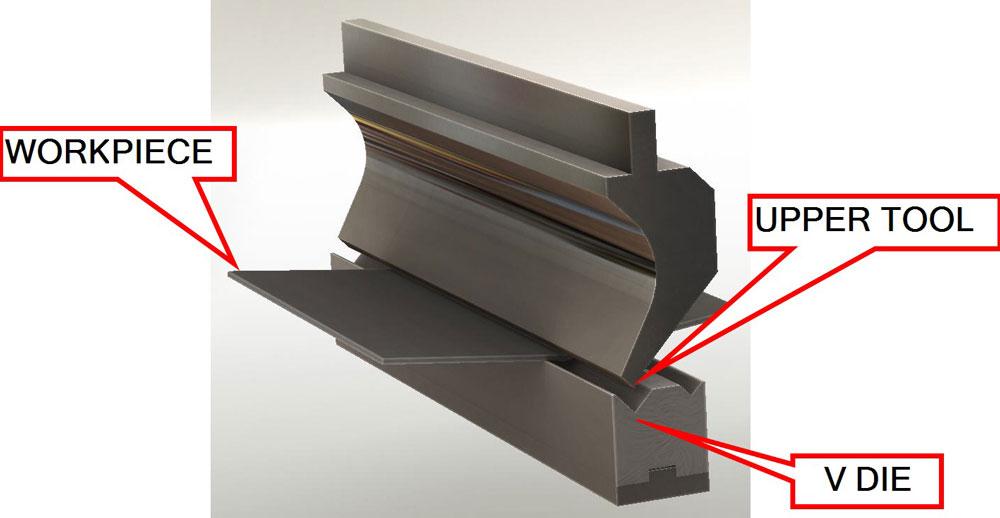
3. Pros
The press brake is equipped with a range of punches and dies, allowing it to be used for processing a variety of workpieces and sheet metals. The press brake excels in producing different types of workpieces in small quantities, such as S-shaped, U-shaped, polygonal, and other shaped products.
Using a press brake tooling storage box can prolong the life of the toolings and lower the cost of production as the toolings are durable and not prone to excessive wear. Additionally, the sheet metal bending machine has a crowning function and can automatically compensate for any discrepancies in the machine.
When dealing with long workpieces, the press brake can also maintain a consistent angle to keep the bend in a straight line, ensuring the accuracy of the final product.
4. Cons
The press brake has a limited tonnage range and can only bend plates within a certain thickness. Plates that are too thick cannot be bent, with a typical maximum plate thickness of 50mm.
After cutting the plate, there may be an oxide layer present, which can cause cracks or fractures during bending. If the bent plate does not match the tooling, creases may form during the bending process, requiring rework or resulting in waste.
If the press brake operates at a stroke speed that is too fast, the operator may not be able to position the plate correctly, leading to defects in the final product or even scrap. It is worth noting that the press brake is limited to bending and cannot perform punching or other processes, serving as a preliminary step in the manufacturing process.
The press brake also requires at least one operator and has a relatively slow bending process, leading to increased time and labor costs in the long run. Additionally, the tolerance for the press brake is not as strict, leading to lower precision in the final product compared to other metal manufacturing machines.
III. What Is Punch Press?
1. Concept and structure
Punching is a metal forming process, and the punch press is a type of machine press that processes metal plates using the punching process. The important parts of the punch press include a frame, which can be C-shaped or door-shaped, a turret, toolings, and a hydraulic cylinder.
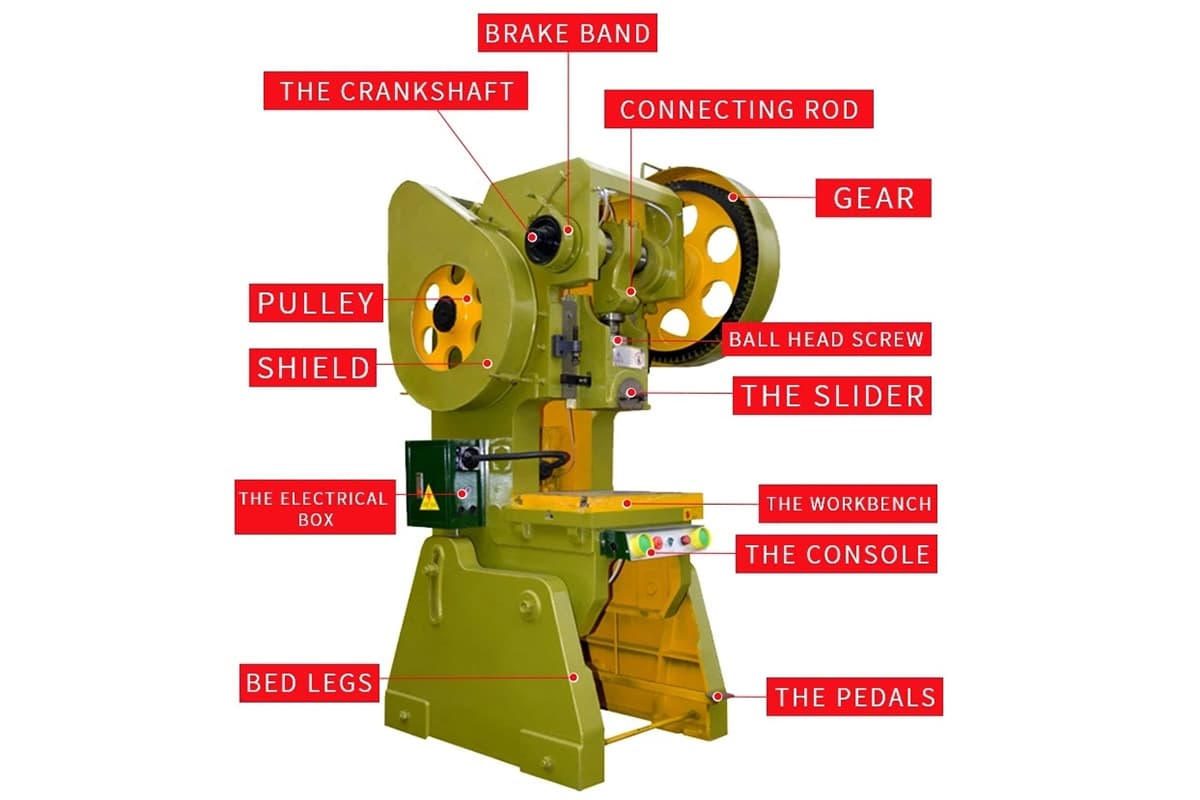
The punch press is utilized to punch or cut holes in the workpiece by driving the punch, with manual and automatic punches being the most common types. When punching, the upper and lower dies are driven by the ram to cut and punch the metal plate, with the shape and size of the die influencing the shape and size of the workpiece.
Materials that can be processed by the punch press include cold-rolled steel, aluminum, copper, and spring steel. There are different types of punch presses, including CNC punch press, pneumatic punch press, hydraulic punch press, and mechanical punch press.
The workpieces produced using a punch press are usually used for electrical appliances, sockets, kitchen supplies, and other products.
2. Pros
The punch press can create precise round or square holes by adjusting the die or stroke. In addition to punching, the punch press can also be used for cutting, which makes it a good alternative to laser cutting machines. The machine is stable and accurate, and is equipped with emergency brakes and light curtain equipment for added safety.
The punch press is durable, as its components including the punch and gear are made of high-strength alloy. It eliminates the need for a secondary forming operation as it completes the forming in a sequential manner during punching.
3. Cons
The punch press generates loud noise during operation, which can be harmful to the operator. The punch press is expensive, consumes a lot of energy, and is time-consuming, and cannot process thick plates.
Customized toolings are costly, as the punch press typically comes with standard size and shape toolings. The toolings wear over time and need to be replaced regularly. The punch press leaves a significant gap between parts during punching, leading to waste of space.
IV. What’s the Difference Between Press Brake and Punch Press?
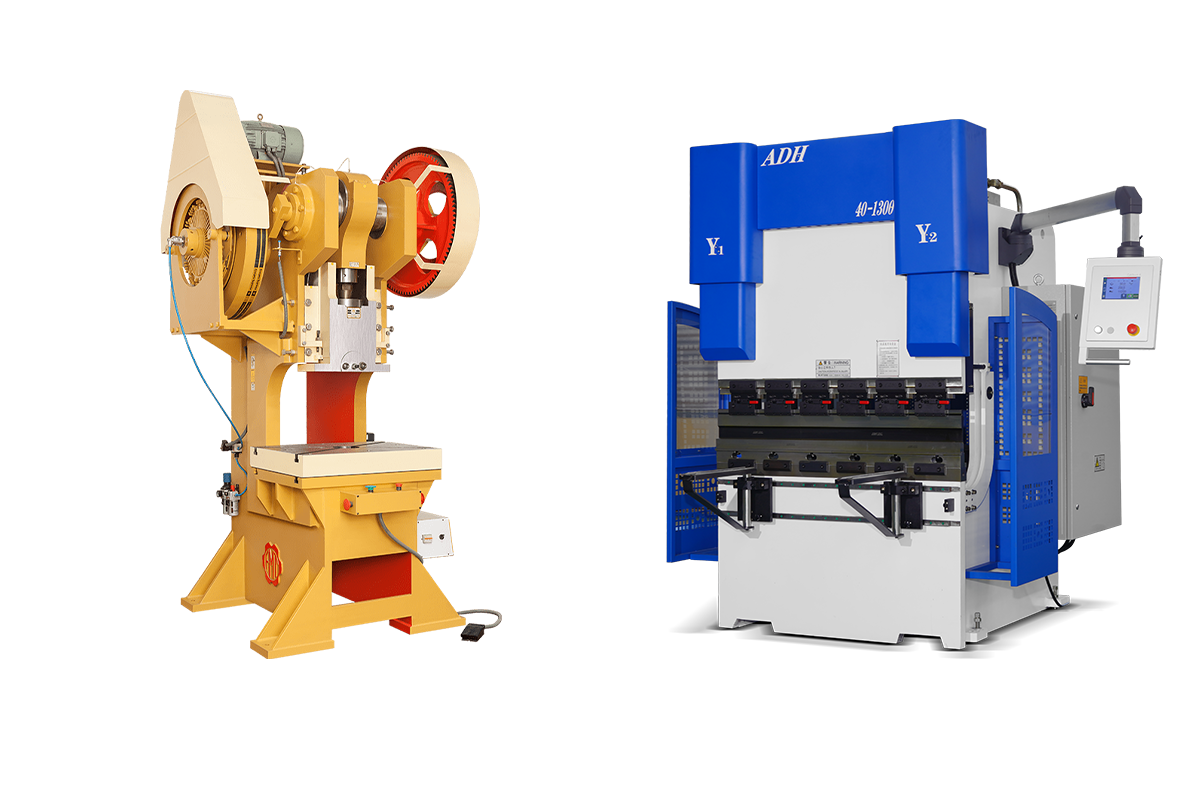
What’s the difference between a press brake and a punch press? The punch press is a machine used for metal punching, marking, cutting, slitting, rolling, deburring, forming, tapping, and countersinking operations. Its versatility arises from the various types of punching tooling that it can accommodate.
A punch press can carry out overall shearing and punching, and some models even come equipped with laser cutting and material feeding devices. The shape of the workpiece is determined by the shape of the punch tooling, some of which can rotate.
After the metal sheet is processed by the punch press, there will be no burr, and the shape of the workpiece will remain intact. However, the punch press is not suitable for turning the workpiece, which makes it not ideal for working on pieces with positive and negative bending.
The punch press's maximum bending angle is typically around 90 degrees, and its tonnage range is relatively small, allowing for the processing of only thin plates. Additionally, the punch press requires a certain clearance during processing, limiting the length of the workpiece that can be processed.
On the other hand, the press brake is primarily used for bending metal plates and has a relatively singular function. It consists of two groups of matching tooling, with the upper die pressing the plate into the lower die under pressure.
The press brake's tooling can be disassembled, but it cannot be moved during the bending process. The press brake's backgauge has multiple axes, which enables accurate plate positioning. The bending angle of the press brake is dependent on the tooling and backgauge, and its bending angle range is much larger than that of the punch press.
The press brake's tonnage range is substantial, ranging from 40T to 1000T, allowing for the processing of thick plates. The length of the workbench limits the length of the sheet that can be processed by the press brake.
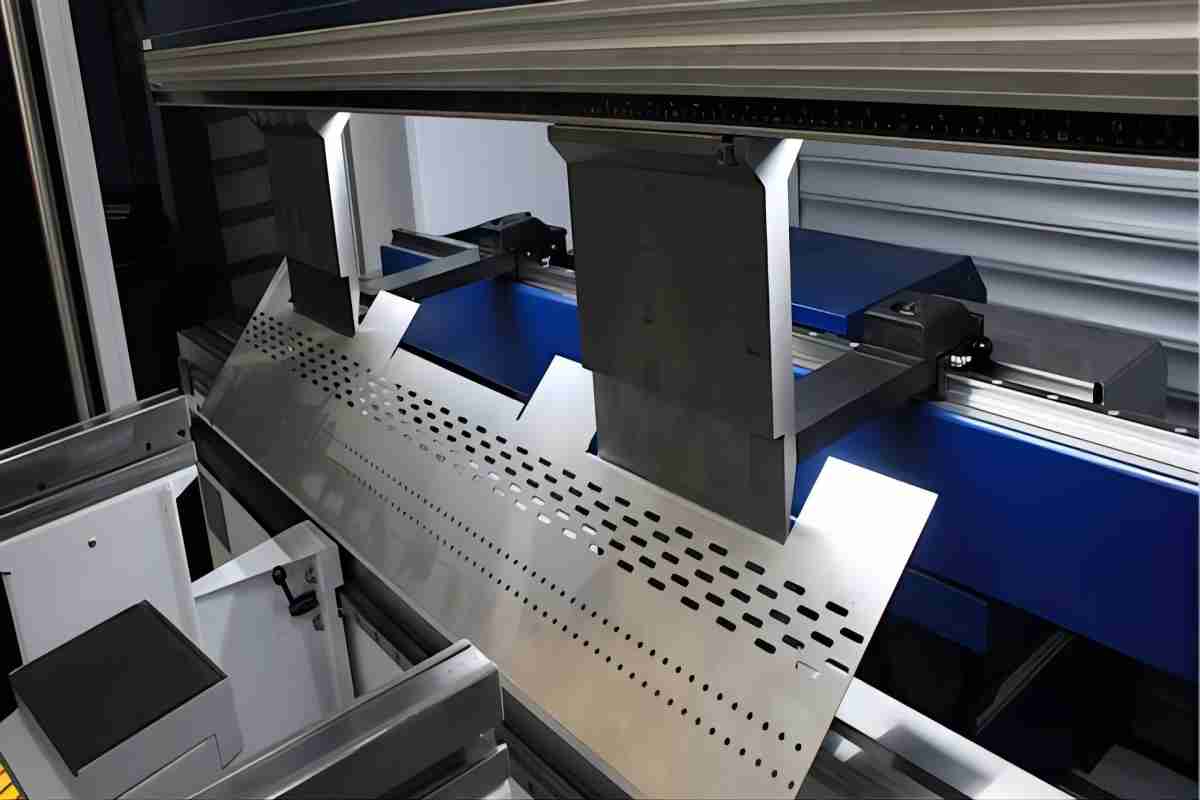
Here is the comprehensive comparison of press brakes and punch presses:
Aspect | Press Brake | Punch Press |
Primary Use | Bending sheet metal into various angles and shapes | Making holes or cutting shapes out of metal sheets |
Versatility | High versatility with various bending angles and depths | Focused on producing identical shapes and patterns |
Precision | High precision, especially with CNC technology for exact angles | High precision in placement and size of holes, particularly with CNC control |
Production Volume | Best suited for low-to-medium volume tasks requiring customization | Ideal for high-volume tasks due to speed and ability to create consistent, repeatable patterns |
Material Handling | Capable of handling a wide range of material thicknesses, including thicker and harder materials | Limited in handling thicker and harder materials, best for thinner materials |
Speed | Slower operation, focusing on precision and quality of bends | High-speed operation, focusing on rapid, repetitive punching |
Complexity of Task | Suitable for complex bending tasks requiring precision and flexibility in angles and depths | Suitable for tasks requiring the creation of identical shapes or patterns at high speed |
Efficiency | Efficient in tasks that demand precision and accuracy, where quality of the bend is more important than speed | Efficient in high-volume applications requiring speed and consistency, such as in the production of electronic parts or appliances |
Cost and Maintenance | Higher initial investment and maintenance costs, especially for CNC models | Generally lower initial investment but higher maintenance costs due to more moving parts and frequent maintenance needs |
Operator Skill Level | Requires skilled operators, especially for CNC models, but modern machines offer user-friendly interfaces | Requires skilled operators familiar with control systems and programming, higher technical skill required |
Application Examples | Aerospace, automotive, construction, heavy machinery manufacturing | Electronics, appliance manufacturing, high-volume production environments |
V. Which One is Better: Press Brake or Punch Press?
While both the press brake and punch press are essential machines in the sheet metal industry, they serve different purposes. The choice between a press brake and a punch press often comes down to the specific requirements of the project..
If you need to produce a workpiece with numerous holes, a punch press would be the ideal choice. A modern press brake would be more suitable for bending plates or making shapes such as boxes or pipes. While the punch press is a more versatile machine, the press brake is still an indispensable tool for metal processing.
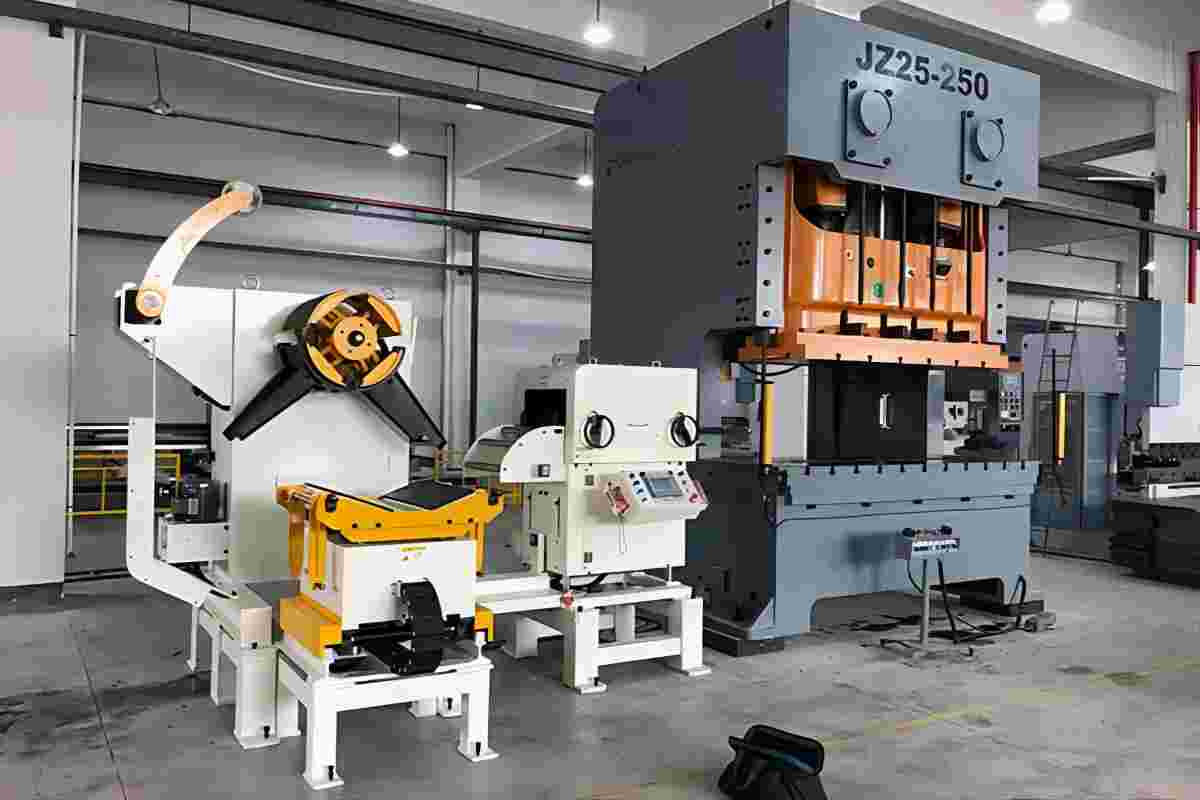
VI. What is the difference between punching and stamping?
There is often confusion between metal punching and metal stamping. Punching machine uses a punch and a die to punch or shear metal plates. The punch passes through the metal plate while the die protects the metal from damage.
Stamping involves processing the metal plate to achieve the desired profile and requires coordination with other processes. If you need to produce a specific shape on the workpiece, punching would be the preferred process.
For full workpiece processing, stamping press would be the better option. Punching is ideal for producing prototypes while stamping is better suited for mass production.
VII. Conclusion
Different sheet metal manufacturing machines are appropriate for producing different parts. Understanding the features and differences between a press brake and a punch can help you make an informed decision.
When faced with the choice of press brake or punch press, factor to consider such as efficiency, cost, ease of operation, and maintenance when selecting a machine. Before making a choice, it is important to familiarize yourself with a company's offerings and services.
ADH Machine Tool offers a wide range of machines in sheet metal fabrication. Browse the product page for details: CNC press brakes, shearing machines, laser cutting machines, panel benders, and other products, or contact our sales manager for further information.
Insulation Powder Coating
HLM Powder Coating CO,.Ltd , https://www.holymepowder.com