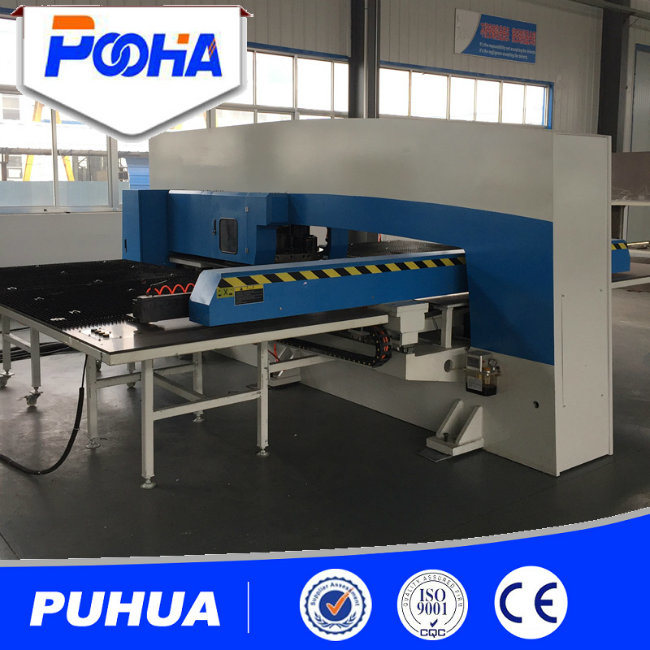
Software:Adopts CACKAD software can realize Auto CAD graphics automatically converts processing procedure, bring their own mold library management, automatic optimization of processing path, realize plank material automatic relocation, plate automatic relocation, no dead zone for processingÂ
2. Stamping body:Fuselage is O type Steel welding, the whole pass by tempering treatment, make sure the equipment good appearance and long-term stability.Â
3. Turret Organization:Adopt high strength nodular cast iron to cast into integral thick turret mold plate, thickness is 80mm, through heat treatment to get rid of internal stress, rigid good, precision stability, impact resistant ability good; greatly improving mold service life;Â
4. Mold: adopts AMADA standard thick turret mold, convenient for daily maintenance and procurement.
5. Motor/drive: Aston high-power servo motor and servo drive system, speed 3000 r/min, high feeding speed, high precision.
6. The transport Ball Screws: Germany Rexroth Ball Screws, attainability 5 grade precision.
7. Guide Rail: Germany Rexroth Linear Guide, With Wider Flange-type Slider to ensure the equipment operating more stability.
8. Orientation Cylinder:Import Korea brand cylinder to achieve precise positioning of the purpose of locking.
9. Reducer: Precision turbine worm reducer, with band-type brake function, reduce the impact to the servo motor after the mold high-speed operating, at the same time guarantee the turret high-speed positioning accuracy; Â Â
10. Clamp:Adopt float type pneumatic clamp, can be together with plates float, avoid plates distortion;
11. Working table: High quality brush steel ball mixed countertops, greatly reduces the friction plate movement, effective protection plate surface; Â
12. Lubricating system:Adopt the automatic control system of oil station, according to the preset time, guide rail, screw etc main transmission mechanism can realize automatic centralized lubrication;
13. Main electrical components:relays, photoelectric sensors, contactor, etc all adopt the Omron and Schneider brand, long-term guarantee the safety of the device;
14. Rotating station: Adopt the standard structure of worm and worm wheel rotating mechanism, the whole mechanism is processed by high precision grinding processing equipment, fully guarantee the centring of upper and lower mold after long-term rotation of rotating station, increase the service life of mold, effectively solve the difficulty of arbitrary Angle punching and trimming.
15. Stamping main servo system: Adopting Rexroth high-power servo motor, punch frequency up to 900 times, punch force stable, using water cooling, the stability is higher.
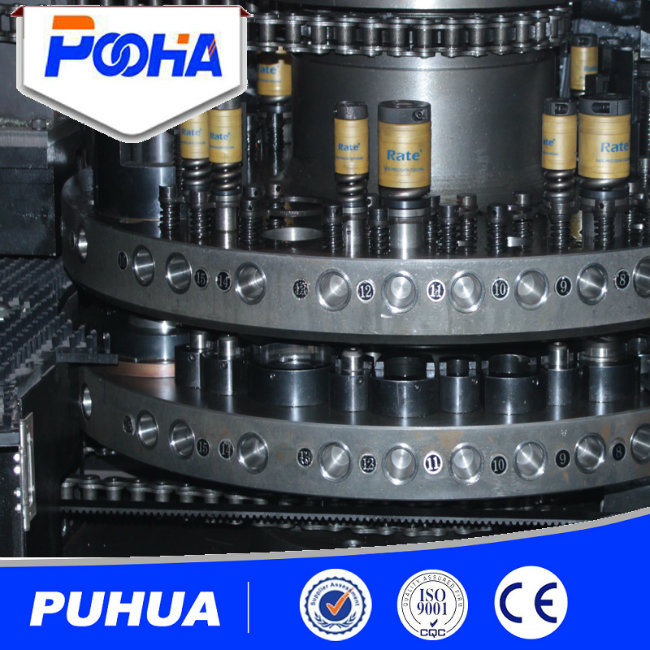
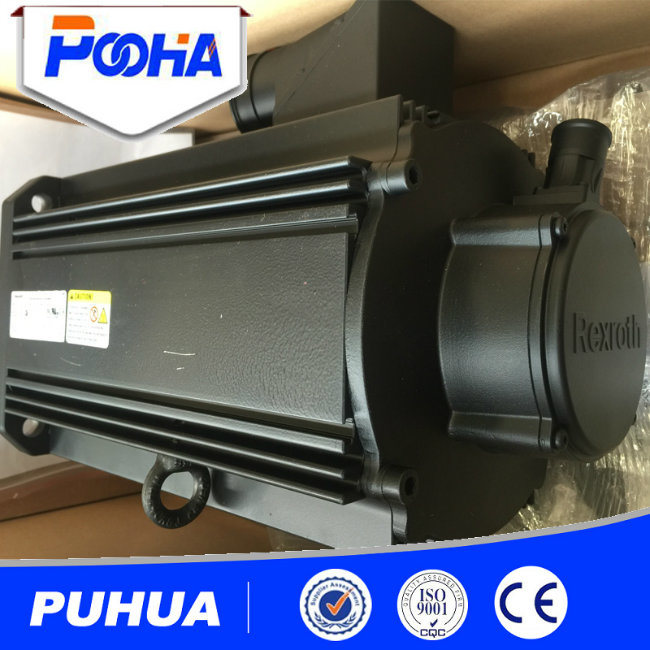
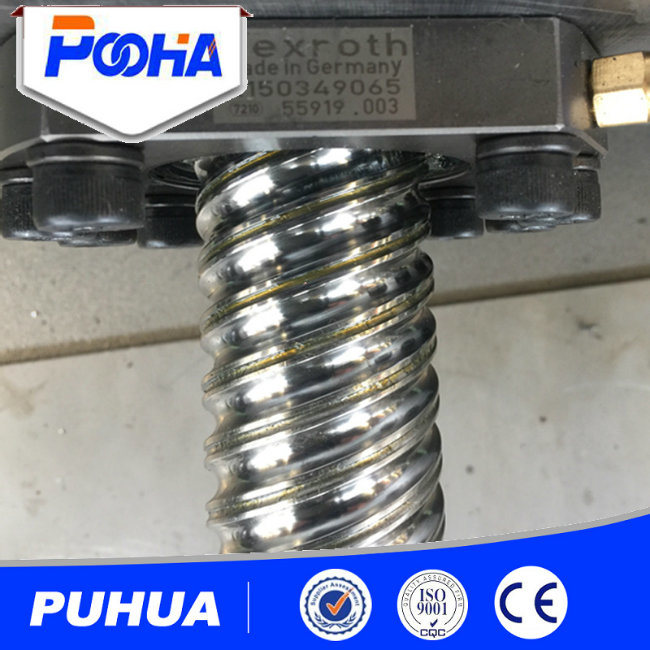
Main Specification:
Specification | Unit | Model Specification | |
AMD-SE2510 | AMD-SE3510 | ||
Punch Force | KN | 200 | 300 |
Max. Processing Size | mm | 1250*2500 | 1250*2500 |
1250*5000 | 1250*5000 | ||
1500*5000 | 1500*5000 | ||
Max. sheet Thickness | mm | 4 | 6 |
Max. Punch Hit | hpm | 1800 | 1800 |
Max. Traversing Speed | m/min | 80 | 80 |
Turret Speed | rpm | 40 | 40 |
Hole Accuracy | mm | ±0.1 | ±0.1 |
Max. Punch Diameter | mm | 88.9 | 88.9 |
Number of stations in turret | / | 24/32 | 24/32 |
Air Pressure | mpa | 0.8 | 0.8 |
Controlled Axis | No. | 5(X,Y,C,P) | 5(X,Y,C,P) |
power rating | KW | 30 | 35 |
Outline Dimension | Mm | 4490*5300*2110 | 4490*5300*2110 |
Machine Weight | Kg | 13 | 14 |
Machinery main details:
1. Germany Rexroth System;
2. AMADA Standard 80mm Ductile Iron Thick Turret Disc;
3. Rexroth Ball Screw & Linear Guide;
4. International electrical components;
5. Secondary positioning system.
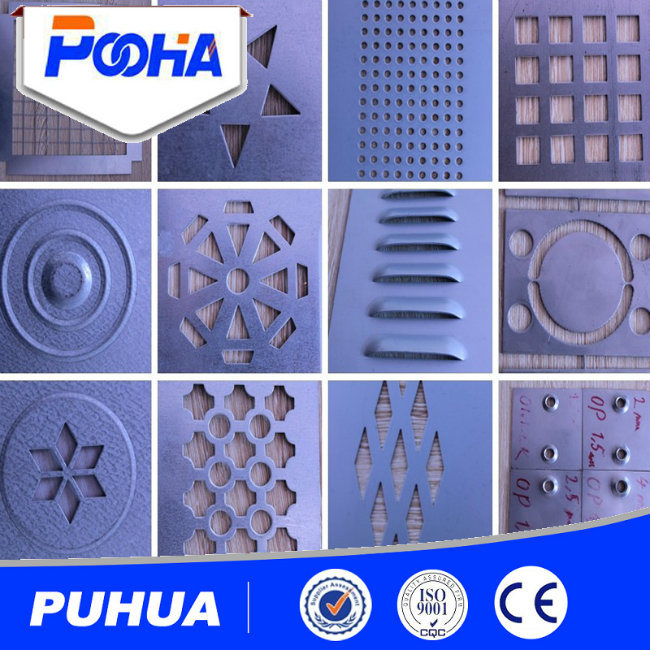
Our service:
1 |
Reply your inquiry in 12 working hours. |
2 | Experienced staffs answer all your questions in time. |
3 | Customized design is available. |
4 | Exclusive and unique solution can be provided to our customer by our professional engineers and staff. |
5 | Special discount and protection of sales are provided to our distributor. |
6 | We are professional manufacturer of sCNC punching Machine. Have a professional design team with more than 10 years design experience engineers, competitive with good quality. |
7 |
As an honest seller, we always use superior raw material, advanced machines, skilled technicians to ensure our products to be finished in high quality and stable feature. |
8 | Prompt delivery, site installation and commissioning. |
1 |
10 years professional production experience in CNC punching machinery industry. |
2 | 22,000 m^2 production workshop, strong production capacity. |
3 | Professional senior engineer develop the best solution. |
4 | Strict quality control system, CE, BV, ISO9001 certificate available. |
5 | Main components adopt imported international famous brand. |
6 | Timely delivery, one hour to Qingdao port. |
7 | Professional after-sale service, Email will be reply in 24 hours. |
8 | Site installation and commissioning in your factory |
According to your requirements, the most suitable machines will be designed for your workpieces, please indicate the following details.
1. Please tell us your metal sheet material.
2. The workpiece dimension (including length, width and thickness).
3. The information of hole shapes and hole diameter that you want to punch.
4. It's my pleasure if you can send some photos or drawings of your products for our reference.
Based on these details information, the detailed technical proposals will be sent to you for reference.
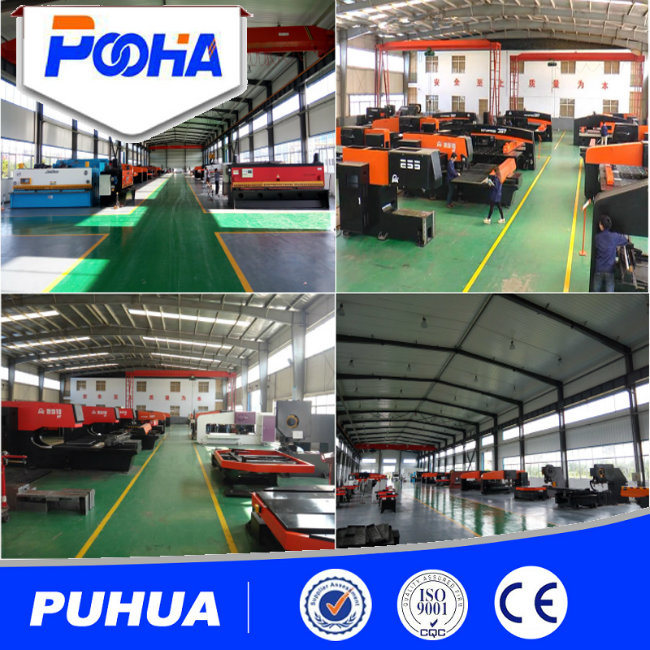
Any question please do not hesitate to contact us.Â
Warmly welcome to visit our factory in Qingdao China.
Tungsten carbide roller has characteristics of good wear resistance, high temperature red hardness, thermal fatigue resistance and thermal conductivity and high strength , have been widely used in high-speed wire rod, bar, rebar, seamless steel tubes, etc. Domestic production of tungsten carbide roller materials mostly WC- Co, WC- Co- Ni- Cr two series, and the content of Co, Co- Ni - Cr is in the range of 6wt% ~ 30wt%. From the use of perspective, tungsten carbide rollers has good mechanical properties, its flexural strength up to 2200 MPa or more, shock toughness up (4 ~ 6) × 10^6 J/ m^2, Rockwell hardness (HRA) is up to 78 to 90, widely in the high-speed wire rod rolling process, which is much higher than single-slot chilled cast steel or high speed steel rolls.Tungsten carbide is made of Tungsten Carbide Powder and binder phase (such as drilling, nickel, etc.), and then pressing and sintering, regardless of the conditions under cold rolled or hot rolled has excellent wear resistance, tungsten carbide rollers has been widely used in pre-finishing mill and finishing of high-speed wire rod currently. On the performance of tungsten carbide roller in hot-rolling wire rod , the material must meet the following requirements:
1. Sufficient anti-fracture strength;
2. Good abrasion resistance;
3. The smooth surface finish;
4. Excellent corrosion resistance, thermal fatigue, thermal cracking performance.
Tungsten carbide roller rings can working in bad conditions , small profile rolling (especially rebar rolling) process conditions is harsher than the high-speed wire rod, and therefore corresponds to the profile rolling ,tungsten carbide rollers recommend using high binder phase carbide.
Tungsten carbide roller material design
Pre-finishing all vehicles roller should ensure its high toughness, strength, rigidity and thermal conductivity, followed before considering its wear resistance. When designing each vehicles roller, pre-finishing materials should choose carbide grades of Co, Co- Ni- Cr binder content is high (greater than or equal to 25wt%) , requiring an average WC grain size of coarse (5μm ~ 6μm), to obtain a higher shock toughness, proper strength and hardness. For the finishing of the roller movements, particularly the last two rollers of the finish rolling, which suffered load is small, and high relative velocity of the material to be pressed (80 m / min ~ 120 m / min). In this case, the wear resistance of the roller to be the most important requirements, and must ensure the strength , timpact toughness and hardness of a reasonable match, so the binder of Co / Ni content ratio and the average grain WC control of particle size and other factors must have greater control in front of different pre-finishing rolling roll.
Tungsten carbide roller category
According to the structure of tungsten carbide rollers, it can be divided into solid tungsten carbide roller and composite tungsten carbide roller. Solid tungsten carbide rollers have been widely used in pre-finishing and finishing stands high speed wire rod mill (including fixed reducing the rack, pinch roller rack). Composite tungsten carbide roller is made of cemented carbide and other materials, and it can be divided into tungsten carbide composite roll rings and solid tungsten carbide Composite Roller. Tungsten carbide composite roll rings mounted on the roller shaft; solid tungsten carbide composite roller will be directly cast in the roll axis to form a whole, a large load is applied to the rolling mill.
Tungsten carbide roller production process control
Tungsten carbide rollers produced by powder metallurgy method, the key to its process control is the chemical composition of the material and the mixture was prepared, pressed molding, sintering and deep processing and other preparation process parameters.
1. Preparation of starting material (WC focus quality): As the WC raw material and quality control of the use of different levels of quality may fluctuate, resulting in adverse effects on microstructure.
2. Preparation of the mixture: Mixture preparation is the key to the production process of the roller, the roller of failure modes - trachoma, mainly generated by this procedure.
3. Pressing: roller pressing is an important process of the roller mill.
4. Sintering: roller sintering is to determine the final quality of the roller production processes, use of advanced low-pressure sintering technology, HIP sintering technology can greatly improve the performance of roller.
5. Deep processing: deep processing rollers have a greater impact on the quality and accuracy of the roller surface.
Carbide Roller,Carbide Ring,Mill of Rolling Line,Steel Wire Rod,Mill Rolling Finish Stand,Mill Roller Groove Type
Luoyang Golden Egret Geotools Co., Ltd , https://www.egretgeotools.com