排队领å·ã€å¡«è¡¨å®¡æŸ¥ã€ä¸Šçº¿æ£€æµ‹ã€äº¤é’±èµ°äººâ€¦â€¦è¿™æ˜¯æ¯ä¸ªè½¦ä¸»æ¯å¹´éƒ½ç»•ä¸è¿‡åŽ»çš„ä¸€ä¸ªè€—æ—¶è€—é’±çš„ç—›è‹¦â€œä»ªå¼â€ã€‚
   æµäºŽå½¢å¼ã€å·§ç«‹å目乱收费ã€å½¢æˆåºžå¤§åœ°ä¸‹ç°è‰²åˆ©ç›Šé“¾â€¦â€¦è¿™æ˜¯ä»Žæœªåœæ¢çš„坹当剿œºåŠ¨è½¦å¹´æ£€åˆ¶åº¦çš„è´¨ç–‘ã€‚
   现行机动车年检的实际效果有多大?为什么一些国家没有“车检â€åˆ¶åº¦ä¾æ—§å¥½å¥½çš„?放宽车检时é™ä¹ƒè‡³å–æ¶ˆè½¦æ£€åˆ¶åº¦æ˜¯å¦æ˜¯å¤§åŠ¿æ‰€è¶‹?
   ä¸å¯æˆ–缺的“车检â€?
   公安部交管局今年1æœˆå…¬å¸ƒçš„æ•°æ®æ˜¾ç¤º:截至2014年底,æˆ‘å›½æœºåŠ¨è½¦ä¿æœ‰é‡è¾¾2.64亿辆,其䏿±½è½¦1.54亿辆;机动车驾驶人çªç ´3亿人,其䏿±½è½¦é©¾é©¶äººè¶…过2.46亿人。
   按照é“路交通安全法åŠå®žæ–½æ¡ä¾‹è§„定,è¥è¿è½½å®¢æ±½è½¦å’Œå¤§åž‹ã€ä¸åž‹éžè¥è¿è½½å®¢æ±½è½¦åˆ†åˆ«5年以内和10年以内æ¯å¹´æ£€éªŒ1次,è¶…è¿‡åŽæ¯6个月检验1次;å°åž‹ã€å¾®åž‹éžè¥è¿è½½å®¢æ±½è½¦6年以内æ¯2年检验1次;超过6å¹´çš„,æ¯å¹´æ£€éªŒ1次。
   “机动车年检相当于是åšä¸€æ¬¡â€˜ä½“检’,ç›®çš„åœ¨äºŽåŠæ—¶å‘现问题,å®žçŽ°é˜²æ‚£äºŽæœªç„¶ã€‚â€æ¹–北çœå®œæ˜Œå¸‚å…¬å®‰å±€äº¤è¦æ”¯é˜Ÿè½¦è¾†ç®¡ç†æ‰€å‰¯æ‰€é•¿é‚“祖波介ç»ã€‚
   天津市交管局安监处负责人表示,对机动车进行检测比较é‡è¦,一年驾龄的驾驶人大概å 到全部驾驶人总数的一æˆä»¥ä¸Š,三年驾龄以下的驾驶人更是å 到了将近四æˆã€‚相对年轻的汽车驾驶人结构,自身并ä¸è¶³ä»¥æ‰¿æ‹…æ±½è½¦å®‰å…¨çš„è¯†åˆ«ã€æ¶ˆé™¤,å¦‚æžœå–æ¶ˆå¹´æ£€,汽车本身å˜åœ¨çš„å®‰å…¨éšæ‚£å°±å¾ˆéš¾è¢«å‘现。
   在公安部与质检总局è”åˆå¬å¼€çš„åŠ å¼ºå’Œæ”¹è¿›æœºåŠ¨è½¦æ£€éªŒå·¥ä½œç”µè§†ç”µè¯ä¼šè®®ä¸Š,有关部门é€éœ²,æˆ‘å›½â€œå¹³å‡æ¯å¹´æ£€éªŒæ±½è½¦7000多万辆次,åŠæ—¶å‘现严é‡å®‰å…¨éšæ‚£è½¦è¾†300多万辆,对预防和å‡å°‘é“è·¯äº¤é€šäº‹æ•…å‘æŒ¥äº†é‡è¦ä½œç”¨â€ã€‚
   耗资巨大检验æµäºŽå½¢å¼
   但在官方数æ®çš„背åŽ,公众看到的更多是车检ä¸å˜åœ¨çš„ç§ç§é—®é¢˜,甚至屡屡引å‘â€œé›†ä½“åæ§½â€ã€‚
   专家测算,æˆ‘å›½å¹³å‡æ¯å¹´7000多万辆次车辆年检,æ¯æ¬¡è½¦è¾†æ£€éªŒéœ€è¦100-200å…ƒ,全国在车辆检测上è¦èŠ±è´¹100多亿元。
   河å—车主å½ä¼Ÿè¯´,æ¯æ¬¡éªŒè½¦éƒ½è¦æŽ’队拥挤,浪费时间。“一大早就到检测场,ç„¶åŽå°±èƒ½çœ‹åˆ°å·²ç»æœ‰ä¸€å¤§å †è½¦åœ¨æŽ’队。æ¯ä¸€é¡¹æ£€æŸ¥éƒ½æŽ’ç€å¤§é˜Ÿ,å³ä½¿è½¦æ²¡ä»»ä½•问题,至少也è¦åŠå¤©çš„æ—¶é—´â€,“纯属浪费时间走形å¼â€ã€‚
   “走过场â€çš„问题更是让人æ¼ç«ã€‚å¤©æ´¥è½¦ä¸»å°æŽæœ‰ä¸€è¾†ç»è¿‡æ”¹è£…的三è±è½¿è½¦,“进排气系统ã€å‘动机ã€è½®æ¯‚ã€åˆ¹è½¦ç³»ç»Ÿå’Œè½¦è½½ç”µè„‘å…¨æ”¹äº†ã€‚â€æŒ‰ç…§è§„定,è¿™æ ·çš„è½¦è¾†è‚¯å®šæ— æ³•é€šè¿‡å¹´æ£€,但实际上他的车æ¯å¹´éƒ½èƒ½é¡ºåˆ©é€šè¿‡å¹´æ£€ã€‚“把别人的车轮æ¢ä¸Š,临时拆掉改装的尾翼,没人会拆开å‘动机看。â€å°æŽè¯´ã€‚
   尤其æ¶åŠ£çš„æ˜¯,在一些地方,车检检测线之外一æ¡åºžå¤§çš„ç°è‰²åˆ©ç›Šé“¾å·²æˆä¸ºâ€œå…¬å¼€çš„秘密â€ã€‚“黑ä¸ä»‹â€â€œè½¦æ‰˜â€ä¹‹ç±»çš„“寄生â€è€…勾结检验部门部分工作人员的问题屡è§ä¸é²œã€‚检验ä¸ä¸¥æ ¼,花钱就能过;有的“黄牛â€çž…准生财之é“办起“代检â€ä¸šåŠ¡ã€‚
   事实上,车检“形å¼ä¸»ä¹‰â€,检测沦为“花架åâ€,æ£ä½¿å¾—车检制度å˜åœ¨çš„å¿…è¦æ€§å¤§æ‰“折扣。
Â Â Â å–æ¶ˆè½¦æ£€æ˜¯å¤§åŠ¿æ‰€è¶‹?
   2014å¹´5月,公安部与质检总局è”åˆæŽ¨å‡ºæœºåŠ¨è½¦æ£€éªŒæ”¹é©æ–°è§„â€”â€”ã€Šå…³äºŽåŠ å¼ºå’Œæ”¹è¿›æœºåŠ¨è½¦æ£€éªŒå·¥ä½œçš„æ„è§ã€‹,试行éžè¥è¿è½¿è½¦6年内兿£€,并推进检验机构社会化。
   以宜昌市为例,以往检验机构没有社会化,å…·æœ‰èµ„è´¨çš„æ£€æµ‹ç‚¹åªæœ‰1å®¶,æ¯é€¢è½¦æ£€é«˜å³°æœŸ,时常出现检测“供ä¸åº”求â€çš„状况,部分车主需è¦é•¿æ—¶é—´ç‰å€™ã€‚ç›®å‰,å®œæ˜Œå…¨å¸‚å·²ç»æœ‰12家具备检测资质的社会化机构。
Â Â Â æœºåŠ¨è½¦æ£€éªŒæ”¹é©æ–°è§„ä¸,放宽了检测时é™,æå‡ºè¯•行éžè¥è¿è½¿è½¦6年内å…予上线检验ã€ç›´æŽ¥é¢†å–æ£€éªŒæ ‡å¿—ã€‚æ¹–åŒ—çœã€å¤©æ´¥å¸‚ç‰å¤šåœ°äº¤ç®¡éƒ¨é—¨æŽ¥å—记者采访时指出,è¿™æ˜¯è€ƒè™‘åˆ°å½“å‰æ±½è½¦äº§å“è´¨é‡ä¸æ–æå‡,许多ç§å®¶è½¦å‡ºè¡Œé¢‘率ä¸é«˜ã€è¡Œé©¶é‡Œç¨‹åå°‘ã€å®šæœŸä¿å…»è¾ƒå¥½ç‰å®žé™…情况,而作出的针对性调整。
   但有观点认为,è½¦æ£€æ–°æ”¿åªæ˜¯è§£å†³äº†éƒ¨åˆ†é—®é¢˜ã€‚æ¦æ±‰å¤§å¦çŸ¥å社会å¦è€…å°šé‡ç”ŸæŒ‡å‡º,éšç€æ¡ä»¶çš„逿¸æˆç†Ÿ,åº”å½“é€æ¥æŽ¢ç´¢å–消车检制度。åŽä¸ç§‘技大å¦å…¬å…±ç®¡ç†å¦é™¢æ•™æŽˆçދ国åŽè®¤ä¸º,对于éžè¥è¿è½¿è½¦ä»Žæ”¾å®½æ—¶é™åˆ°æœ€ç»ˆå–消车检制度,应该是大势所趋,å› ä¸ºéžè¥è¿è½¿è½¦çš„车检更多体现的是“对自己负责â€ã€‚
   事实上,æ”¾å®½ä¹ƒè‡³å–æ¶ˆè½¦è¾†å¹´æ£€åˆ¶åº¦åœ¨çŽ°å®žä¸ä¼¼ä¹Žå¹¶ä¸æ˜¯é—®é¢˜ã€‚比如,美国的车检是由å„州自己管ç†è´Ÿè´£çš„,部分州没有汽车年检的立法,法国新车å‰4å¹´ä¸éœ€å¹´æ£€,åŠ æ‹¿å¤§åˆ™æ²¡æœ‰å¹´æ£€ä¹‹è¯´ã€‚
Â Â Â ä½†å–æ¶ˆè½¦æ£€äº¦ä¸ä¹å对æ„è§,ä¸å°‘äººå¯¹äºŽå–æ¶ˆæ±½è½¦å¹´æ£€æ˜¯å¦ä¼šå¢žåŠ äº¤é€šå®‰å…¨äº‹æ•…å¿ƒæ€€é¡¾è™‘ã€‚å…¬å®‰éƒ¨æ•°æ®æ˜¾ç¤º,2013å¹´,免国仿œ‰133.8万辆大ä¸åž‹å®¢è´§è½¦é€¾æœŸæœªè¿›è¡Œå®‰å…¨æ£€éªŒã€‚在人员伤亡事故ä¸,有6790起是由于机动车安全性能ä¸åˆæ ¼å¯¼è‡´çš„,é€ æˆä¸€ä¸‡å¤šäººä¼¤äº¡ã€‚
   ç†ä¸è¾©ä¸æ¸…,事ä¸é¢å¯¹ä¸è¡Œã€‚或许,å–æ¶ˆéžè¥è¿è½¦è¾†å¹´æ£€ä¸å¯èƒ½ä¸€è¹´è€Œå°±,但在专家和公众广泛讨论的基础上,ç›´é¢é—®é¢˜,完善调整,åŠæ—¶å¥‘åˆç¤¾ä¼šçš„å‘å±•å’ŒçŽ°å®žçš„è¦æ±‚,而éžå›ºå®ˆæ—¢æœ‰åˆ¶åº¦,一æˆä¸å˜,æ— ç–‘æ˜¯å¿…é¡»çš„ã€‚
Welding Sheet Metal
Sheet Metal Welding
Welding, by definition, is the process of joining two metals together by heating the metal surfaces up to their melting points. However, the process of welding isn`t as simple as it sounds. Welding is a highly technical process, with numerous types and techniques that only skilled personnel are able to understand and practice
Considerations for welding
ï¬Heat: Different types of materials are also subject to distortion. This is the case with thinner ones. Warping can also occur if the heat is too high
ï¬Process selection: In order to avoid the usual problems that come with welding thin metal, you should carefully consider the process you are using.
ï¬Equipment: need to consider the equipment that used and choose the right method to weld.
Welding sheet metal methods
MIG Welding
ï¬What is MIG welding?
Metal Inert Gas (MIG) is also known as gas metal arc welding (GMAW). This type of welding is basically an arc welding process that joins two metals. This is done by heating the metals with the help of an arc. This arc is formed between the surface to be welled and a continuously fed filler electrode. This type of welding uses a shielding gas to protect the molten pool of weld metal from reacting with elements present in the atmosphere. MIG welding requires a DCEP (Direct Current Positive Electrode), also known as Reverse Polarity
ï¬What Metals Can Be MIG-Welded?
One of the major reasons why MIG welding is so common is that it can be used to weld any metal (almost). Although the weld quality from MIG welding is not superior to other types of welding, MIG welding is one of the fastest and the most cost-efficient welding processes. Moreover, MIG welds are great, if not perfect.
The metals that are most commonly welded by this type of welding include stainless steel, carbon steel, and aluminum, with carbon steel being the easiest metal to MIG weld.
ï¬Applications of MIG Welding
Some of the most important applications of MIG welding are listed below:
a)The most common application of MIG welding is in the automotive industry. No matter what the size of the vehicle is, MIG welding is employed for automotive repairs. The reason why MIG welding is the top choice for automotive repairs is that it provides sturdy and robust welds up to a mark of 0.5mm.
b)It is used in sheet metal welding
c)MIG welding is used in pipe welds. Not only does it form efficient and long-lasting welds but it also saves on time and cost
ï¬Advantages of MIG Welding
The use of MIG welding is widespread for all the right reasons – high-quality welds for non-ferrous and ferrous alloys at a fairly low price. It is associated with numerous benefits:
a)It has the ability to join many types of materials
b)It can join materials of different thicknesses
c)The equipment components are simple, and thus, readily available in the market at very affordable prices
d)The electrode efficiencies of MIG welding are higher (92-98%) as compared to other types of welding
e)MIG welding is associated with higher operator factor and welder efficiencies
f)It can be easily adapted for hard automation, high-speed robotic, and semi-automatic applications
g)MIG welding comes with the capability of all-position welding
h)The appearance of weld bead formed from MIG welding is excellent
i)The hydrogen weld deposit in MIG welding is lower
j)It requires a lower heat input as compared to other types of welding
k)The slag and weld spatter is kept at a minimum in MIG welding, which makes the cleaning of the weld easy and quick
l)Less amount of welding fumes are produced in MIG welding which makes it safer for welders
m)The cost of weld metal/ length deposited is lower making MIG welding a cost-effective welding process
n)The skill level needed for MIG welding is lower than what`s needed for other types of welding, making it suitable for beginners
o)The welding wire in MIG welding runs continuously with lesser downtime for electrodes replacement
p)MIG welding is excellent for tack and spot welds
TIG Welding for Sheet Metal
TIG (Tungsten Inert Gas) welding sheet metal is certainly one of the most common welding methods. This is an arc welding process with an infusible (tungsten) electrode, protected by inert gas (the gases most commonly used are argon or helium), which can be performed with or without filler metal
What is the thinnest sheet metal that can be welded?
A welder should approach welding thin materials with caution. You should also take into account the type of material and the welding process you are planning to implement. Gas metal arc welding (GMAW) is a very effective method in joining together thinner materials. So, for instance, you can work on 18-ga. to 0.1875-in. stainless steel or 24-ga. to 0.1875-in. carbon steel.
How do you stop a weld distortion?
Sometimes when welding sheet metal, distortion can occur due to the thickness of the material. Even something minimal likes to patch a panel can end up with devastating effects. The best way to prevent this is to avoid creating distortion as much as possible.
Some methods include:
ï‚·Size of weld: Avoid overwhelming when making a weld seam.
ï‚·Intermittent welding: Try making breaks instead of a single long weld.
ï‚·Fewer weld passes: The more weld passes a welder makes the greater the chance of shrinking the materials. Try making less.
ï‚·Welding placement: You should weld near the neutral axis or the center or the part.
ï‚·Backset welding: A welder should weld from left to right, placing every weld seam from left to right rather than the opposite way.
ï‚·Preset parts: Make trial welds before you start the process by setting the parts together.
ï‚·Use clamps: Clamps are a good way to use instead of a tack weld. You simply clamp down the parts and set them in the desired way before you start welding.
ï‚·Thermal stress relief: The process involves controlled heating of the weldment followed by controlled colling afterward.
ï‚·Minimize welding time: The more time you take to weld a panel the greater the chances are of creating distortion. Simply try shortening the time needed to weld
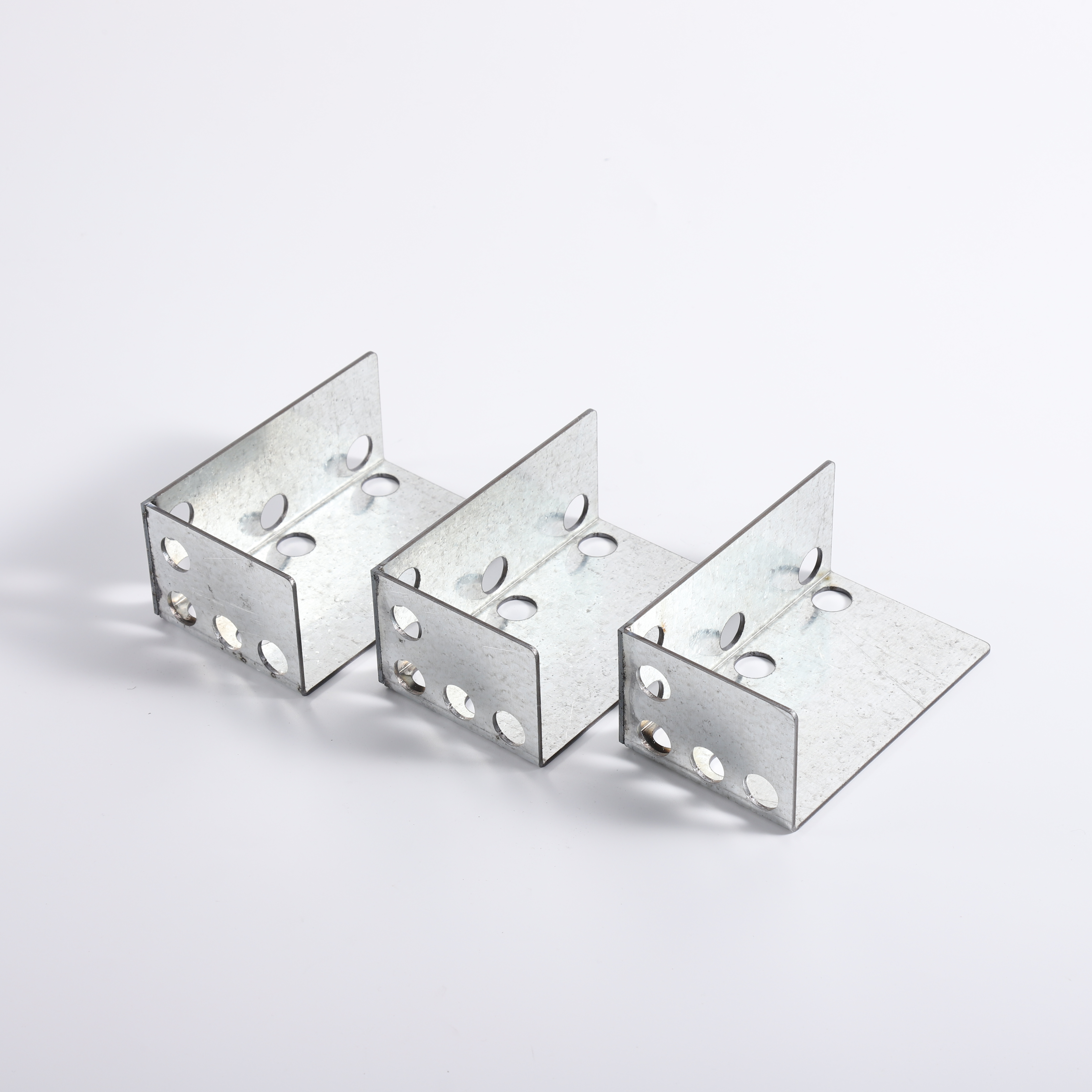
Welding Service,Specialty Welding Services,Laser Welding Services,Custom Welding Services
Suzhou FCE precision electronics Co., LTD , https://www.fukeyifcesz.com