Diaphragm valves (or membrane valves) consists of a valve body with two or more ports, a diaphragm, and a "weir or saddle" or seat upon which the diaphragm closes the valve. The valve is constructed from either plastic or metal.
Â
Originally, the diaphragm valve was developed for use in industrial applications. Later on the design was adapted for use in the bio-pharmaceutical industry by using compliant materials that can withstand sanitizing and sterilizing methods.
There are two main categories of diaphragm valves: one type seals over a "weir" (saddle) and the other (sometimes called a "full bore or straight-way" valve) seals over a seat. The weir or saddle type is the most common in process applications and the seat-type is more commonly used in slurry applications to reduce blocking issues but exists also as a process valve. While diaphragm valves usually come in two-port forms (2/2-way diaphragm valve), they can also come with three ports (3/2-way diaphragm valves also called T-valves) and more (so called block-valves). When more than three ports are included, they generally require more than one diaphragm seat; however, special dual actuators can handle more ports with one membrane.
Diaphragm valves can be manual or automated. Their application is generally as shut-off valves in process systems within the industrial, food and beverage,pharmaceutical and biotech industries. The older generation of these valves is not suited for regulating and controlling process flows, however newer developments in this area have successfully tackled this problem.
In addition to the well known, two way shut off diaphragm valve, other types include: Three way zero deadleg valve, sterile access port, block and bleed, valbow and tank bottom valve.
Media |
water, oil, steam, liquid etc. |
Medium Temperature |
-10°C~180°C |
Pressure |
0.2~2.5Mpa |
Material |
stainless steel |
Port size |
1/2″~ 8″ |
Orifice |
DN15-200 |
ATÂ actuator |
single action/dual action |
Seal |
PTFE |
Voltage tolerance (AC) |
±10% |
Voltage tolerance (DC) |
±1% |
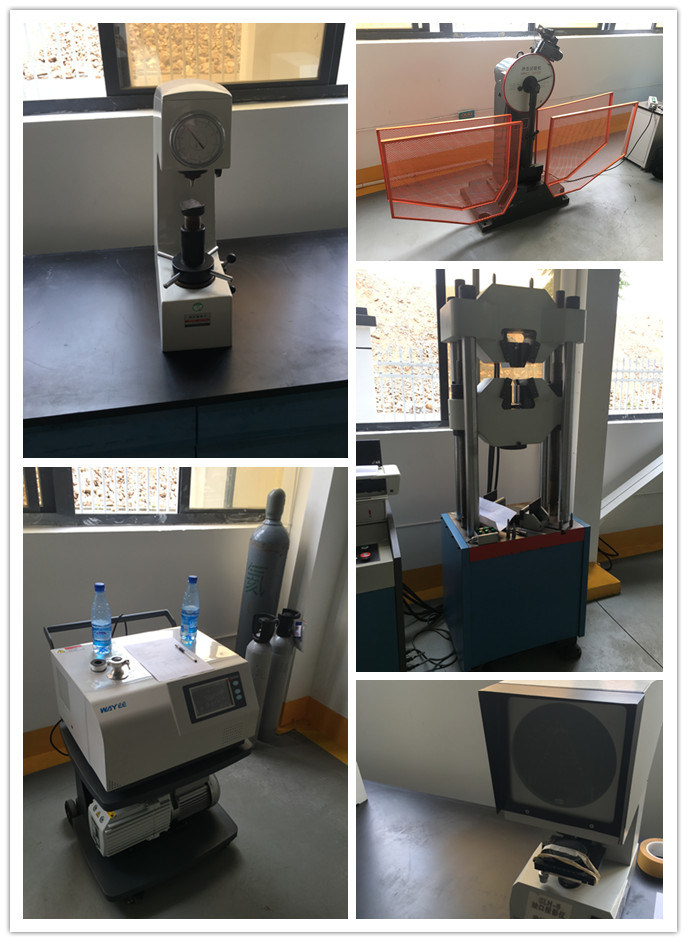
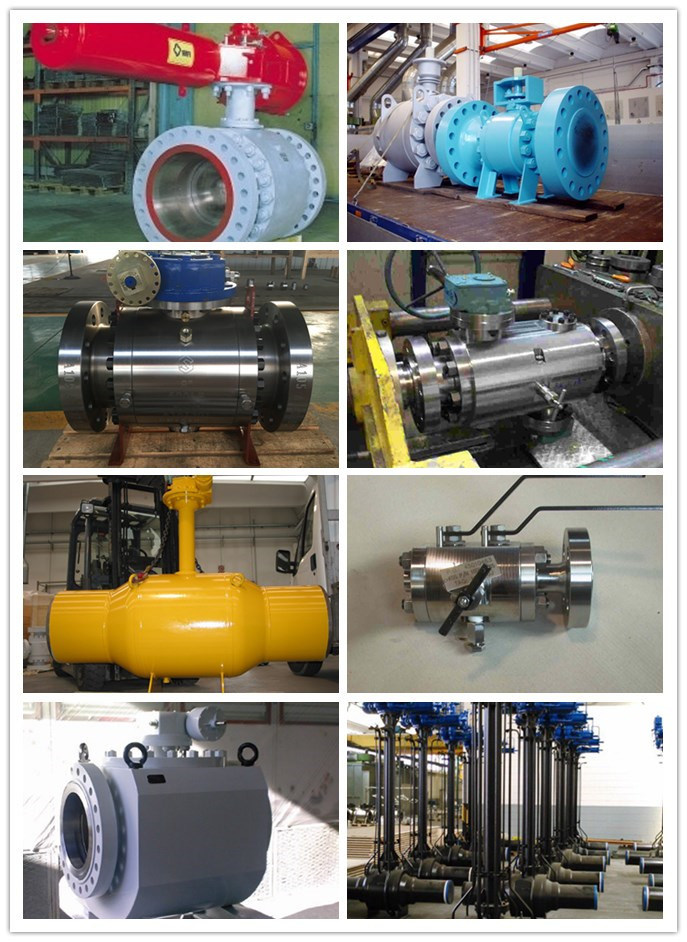
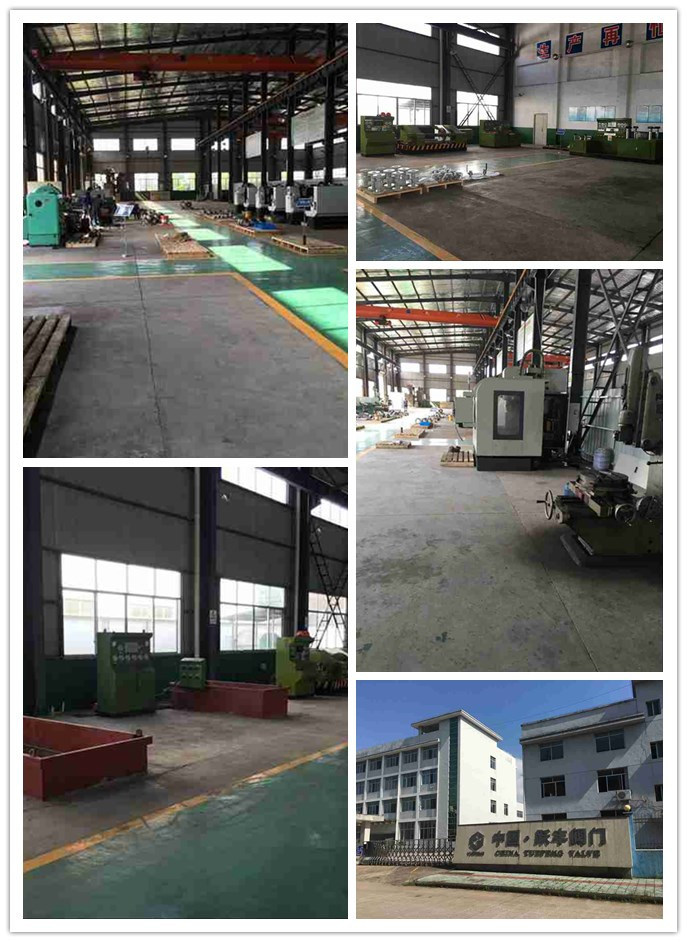
Diaphragm valves (or membrane valves) consists of a valve body with two or more ports, a diaphragm, and a "weir or saddle" or seat upon which the diaphragm closes the valve. The valve is constructed from either plastic or metal.
Â
Originally, the diaphragm valve was developed for use in industrial applications. Later on the design was adapted for use in the bio-pharmaceutical industry by using compliant materials that can withstand sanitizing and sterilizing methods.
There are two main categories of diaphragm valves: one type seals over a "weir" (saddle) and the other (sometimes called a "full bore or straight-way" valve) seals over a seat. The weir or saddle type is the most common in process applications and the seat-type is more commonly used in slurry applications to reduce blocking issues but exists also as a process valve. While diaphragm valves usually come in two-port forms (2/2-way diaphragm valve), they can also come with three ports (3/2-way diaphragm valves also called T-valves) and more (so called block-valves). When more than three ports are included, they generally require more than one diaphragm seat; however, special dual actuators can handle more ports with one membrane.
Diaphragm valves can be manual or automated. Their application is generally as shut-off valves in process systems within the industrial, food and beverage,pharmaceutical and biotech industries. The older generation of these valves is not suited for regulating and controlling process flows, however newer developments in this area have successfully tackled this problem.
In addition to the well known, two way shut off diaphragm valve, other types include: Three way zero deadleg valve, sterile access port, block and bleed, valbow and tank bottom valve.
Media |
water, oil, steam, liquid etc. |
Medium Temperature |
-10°C~180°C |
Pressure |
0.2~2.5Mpa |
Material |
stainless steel |
Port size |
1/2″~ 8″ |
Orifice |
DN15-200 |
ATÂ actuator |
single action/dual action |
Seal |
PTFE |
Voltage tolerance (AC) |
±10% |
Voltage tolerance (DC) |
±1% |
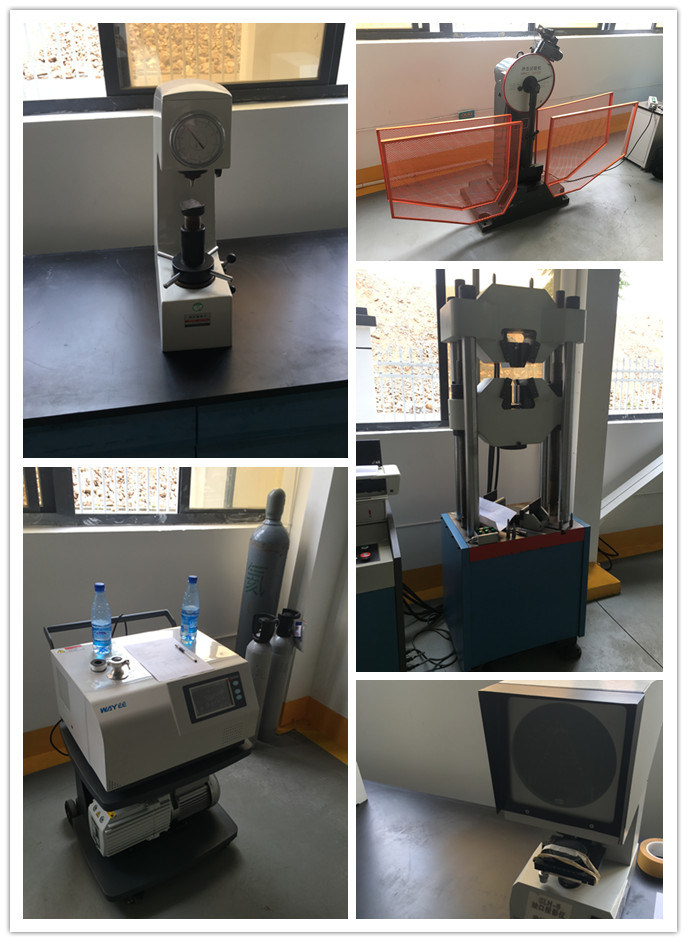
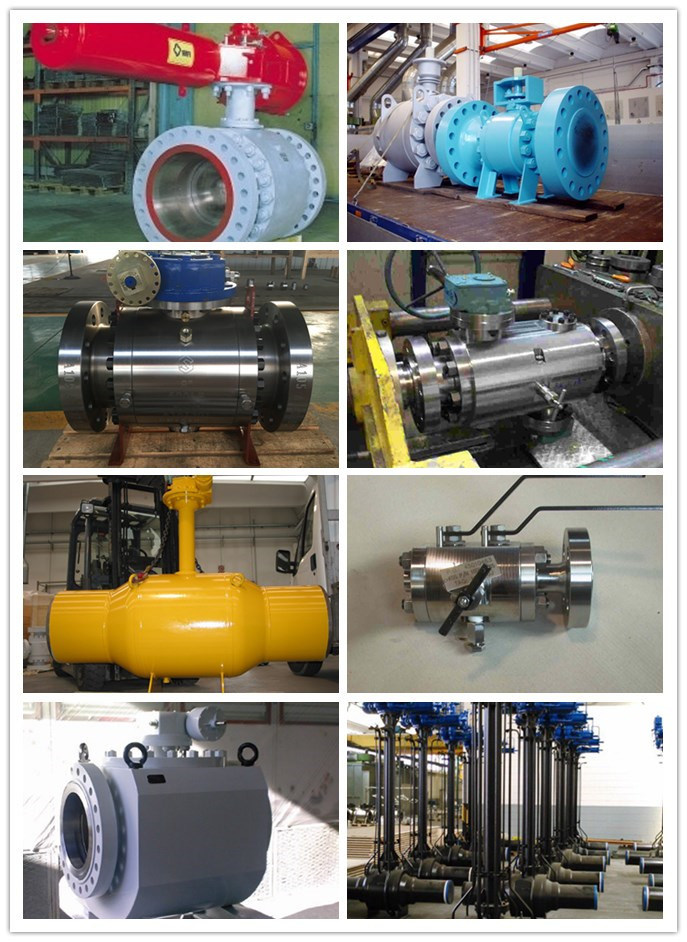
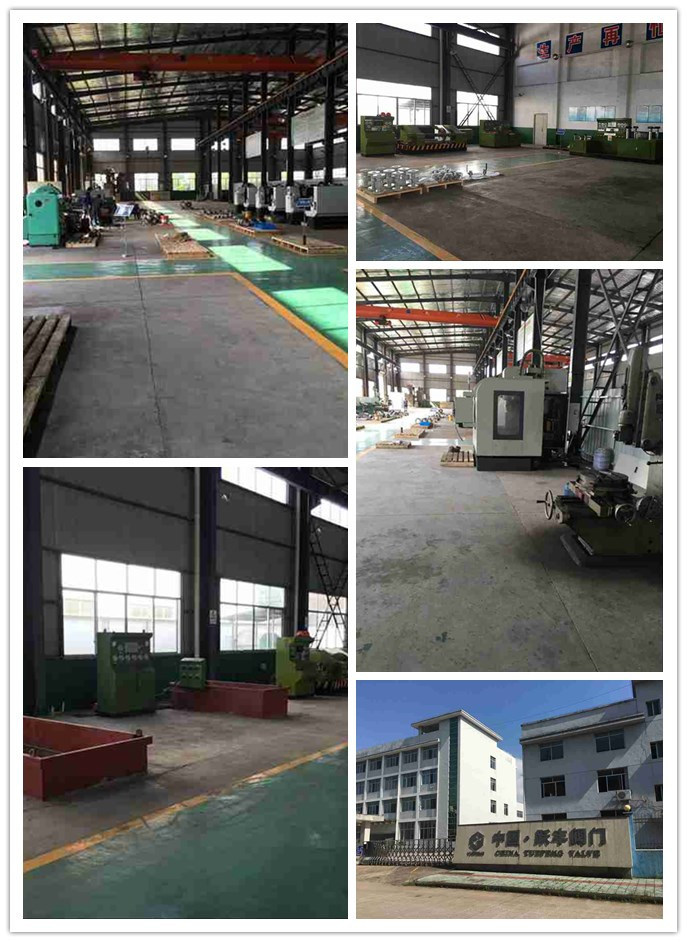
The Chicken Evisceration process is the procedure and equipment required to remove the intestinal pack, recover the edible offal,the cleaning and cooling facilities - all of which are supplied by Connect Equipment. Connect manufacture the semi automatic evisceration line by our own company, the capacity which is from 300BPH to 10,000BPH processing line. This optional is fit for the market where the workers salary is not very high. The process can be completed with some manual pneumatic tools. CONNECT also supply the automatic evisceration machines from worldwide to realize the fully automatic processing system. So whatever you like, we will try our best for helping you.
in this area, it contains evisceration conveyor line, viscera through,carcass washer,automatic evsceration system(vent cutter,opener,cropping machine,Final inspection machine,Offal pump station,Gizzard splitter,Gun for lung replacement ,Vaccum system).so please trust our equipment, it meet different requirements of yours.
Chicken Evisceration Machine, Automatic Chicken Evisceration Machine, Manual Chicken Evisceration, Chicken Cropping Machine,Chicken Evisceration
Connect Group For Poultry Project , https://www.connectpoultry.com