High-chromium white cast iron is a kind of anti-corrosion and wear-resistant material with high hardness and strength. Its tensile strength is 650-850 MPa, its as-cast hardness is HRC 48-55, and its quenched hardness is HRC 55-62. However, this kind of material is hard and brittle, and the cutting state is extremely unstable. If it cannot solve the cutting processing problem well, its application will be greatly limited. Tests show that the use of carbide tools for processing high-chromium cast iron, the tool wear is very fast, the cutting is easy to form a chipping cutting, the surface roughness, can only be used for general roughing. For high-chromium cast iron finishing, lower roughness can be achieved with ceramic tools. However, the impact resistance of ceramic tools is relatively weak, and the brittle materials used for cutting high-chromium cast iron are more vulnerable to impacts and cause tool failure such as chipping. Because ceramic tools are more expensive, they should be avoided as far as possible. Therefore, the correct and reasonable choice of cutting amount is an effective way to avoid the impact damage of the tool. In this paper, under the condition of considering the economical efficiency of tool dynamics, the cutting amount of the outer circle of high-chromium cast iron slurry valve valve plate parts with composite ceramic tool was optimized. 1 Influence of cutting temperature on the dynamic performance of composite ceramic tools The influence of cutting temperature on tool dynamic performance is mainly reflected in the mechanical properties of cutting tool materials and the additional thermal stress generated by the cutting temperature field. The effect of temperature on the mechanical properties of composite ceramic tools The physical and mechanical properties of composite ceramics are generally reduced as the cutting temperature increases. Tests show that within a certain range, when machining steel parts, the mechanical performance indicators and temperatures of composite ceramic tools have the following empirical formula: sbt=sbo(1-bt) (1) sst=ssoexp(1-ct) (2) Et=Eoexp(-dt) (3) Ht=Ho(1-kt) (4) Where: sbt, sst, Et, Ht are the tensile strength, yield limit, and elasticity, respectively, of the composite ceramic tool at temperature t. Modulus and hardness: sbo, sso, Eo, Ho are the tensile strength, yield limit, elastic modulus, and hardness at room temperature, respectively: b, c, k, and d are constants determined by the test. Additional thermal stress generated by the cutting temperature field In continuous turning, when the cutting amount and the external environmental conditions are constant, it can be considered that there is a steady-state heat source on the front and back surfaces of the cutter, and the cutting temperature field on the cutter can adopt three-dimensional thermal conduction. Finite element method calculation. Because the tool is working in the elastic range, the additional thermal stress caused by temperature is st = at (t-t0) E (9) where: t0 is the temperature without stress: at is the coefficient of linear expansion of the composite ceramic. 2 Dynamic stress and dynamic strength of composite ceramics The dynamic stress of the composite ceramic tool is calculated using three-dimensional finite element method. The model is shown in Fig. 1. The cutting force Fz acts in the middle of the cutting edge. The unit adopts an eight-node three-dimensional block element. The contact edge between the tool and the tool body is elastically restrained, and the rest are free edges. Calculating the maximum stress under this condition is exactly the same as solving the general solid mechanics, but considering the effect of temperature, there are

(10) The elastic matrix is ​​constructed by this set of equations and the finite element solution is used to obtain the maximum dynamic stress smax of the tool under the combined action of the cutting force and the temperature field. If the ceramic tool has a rake face temperature of t, the strength is [st ], its dynamic strength condition is smax ≤ [st] (11)

Figure 1 Stress contour map

Figure 2 Calculation block diagram
3 Optimized calculation of cutting amount of composite ceramic tool material The optimization calculation of the objective function cutting amount is based on the processing cost as a target function. The generation of a part mainly includes the following costs: Material cost (Cc) Cost of forming a part blank: Machine tool cost (Cj) Machine work unit cost, including the depreciation of the machine tool, etc.: Cost of tooling (Cg) Unit labor wages for production workers and management and support staff: The total cost of changing a knife and grinding knife (Cd) to produce a part is Cw=Cc+(Cj +Cg)(tz+tj)+Cdtj/T (12) Where: tz is the preparation time: tj is the effective cutting time: T is the tool life and the unit is min. Calculated by Taylor formula T=CV+V-1/mf-1/nap-1/p (13) Basic cutting time tj=kV(Vfap) (14)
In the above two formulas: CV is a constant: ap is the margin. Substituting Equation (13) and Equation (14) into Equation (12) gives Cw=Cc+tzCm+kvCm/(Vfap)+kvCd/[CVf(-1/n)+V(1-1/m)ap(1) -1/p)] (15) Where: Cm=Cj+Cg. Formula (15) is the cost objective function of the tool cutting optimization calculation. Constraint functions The optimization functions for the cutting amount calculation mainly include the following aspects: Cutting consumption constraints. If the machine's cutting speed and feed rate are in the range of (Vmax, Vmin), (fmax, fmin), then the following constraint function G1(f,V)=V-Vmax≤0 (16) G2(f) V)=Vmin-f≤0 (17) G3(f,V)=fmax-f≤0 (18) G4(f,V)=f-fmax≤0 (19) Accuracy constraint. If the given surface roughness is Ra, then there is a constraint function G5(f,V)=f−(8Rar)1â„2≤0 (20) Machine power constraints. If the allowable power of the machine tool is p, the following constraint G6(f,V)=VFz1+zfFzy-p/CFzaKFz≤0 (21) Tool life constraint G7(f,V)=V1/mf1/nap1/ p-CV/T0 ≤ 0 (22) In the above formulae, XFz, yFz, KFz, CFz are experimental constants. Tool dynamic strength constraint function G8(f,V)=smax-st≤0 smax is the maximum dynamic stress calculated by the finite element method for the cutting amount. Optimized calculations Because the tool's maximum dynamic stress is calculated using finite elements, there is no quantitative analytical function. In the optimization calculation, the constraint function G8 cannot be introduced. Therefore, we do not consider G8 in the calculation and optimize a group of cutting amounts. Then we optimize the cutting amount according to this group and calculate the maximum dynamic stress of the tool by the finite element method. If the dynamic strength is satisfied, the cutting amount is optimal. If it is not satisfied, the cutting amount is reduced until the dynamic strength is satisfied. The cutting amount parameter obtained at this time is the most reasonable cutting amount. The calculation diagram is shown in Figure 2.

Figure 3 Tool geometry 4 Calculation results and test raw parameters Machine: CA6140, speed range, N = 12 ~ 1200r/min, feed rate range f = 0.08 ~ 1.59mm/r, power P = 7.5kW. Tool: AG2 composite ceramics, mechanical parameters: e=4550kg/m2, thermal conductivity 22.93W/m·k, thermal expansion coefficient a=8×10-6 (°C)-1, bending strength sb=800MPa, elastic modulus E=420 GPa, Boson's ratio μ=0.24, hardness HV2400. Geometric parameters: g0=-5°, a0=12°, ls=-6°, negative chamfer 30°, width 1mm, tool nose radius r=1mm, dimensions shown in FIG. 3 . Workpiece: Slurry valve, surface roughness Ra = 1.6, material is a new type of chromium high white cast iron, strength 680 ~ 800MPa, diameter 300mm, thickness 40mm, unilateral margin 3mm. Economic parameters: machine tool cost, Cm = Cj + Cg = 42 yuan / min, the cost of tool change and sharpening Cd = 4.8 yuan. Preparation time tz=1.5 minutes, Cc=130. (The above parameters are provided by Wuhan Hailian Machinery Factory). Other parameters: m=0.23, n=0.57, p=1.33. Durability T0=60 min, h=0.75, zFz=0.15, CFy=244, CFz=436, CV=2.28×103, xFy=0.9, yFy=0.55, zFy = 0.3 (The above parameters are AKCnattopadnyay's "Ceramic tool wear characteristics in the cutting of cast iron and steel materials" and the test results). The optimization calculation substituting the above parameters into the objective function and the constraint function can be obtained. The cost objective function is CW=136.3+332.506V-1f-1+2.229V×4f0.75 (23) Each constraint function is G1(f,V)=V- 565≤0 (24) G2(f,V)=0.565-V≤0 (25) G3(f,V)=0.08-f≤0 (26) G4(f,V)=f-1.59≤0 (27) G5(f,V)=f-0.113≤0 (28) G6(f,V)=V0.85f0.75-49.5≤0 (29) G7(f,V)=V5f1.75ap0.75-2.27× 1011 ≤ 0 (30) Calculated with the monte-Cono algorithm to obtain the minimum cost cutting amount is V = 109.8 m/min, f = 0.1 mm/r. Calculate the temperature field with finite element under this cutting amount and see Fig. 1, know from the experience formula, the concentrated force acting on the tool at this moment is Fz = 436* 2* 0.10.75* 109.8-0.15 = 92.016kg Fy = 244* 20.9×0.10.6×109.8-0.3=29.28kg The finite element method is used to calculate the stress under the combined action of the cutting force Fz, Fy and the temperature field as shown in Fig. 2. From the calculation results, we can see that the tool dynamic strength meets the requirements. Cutting speed V = 109.8m/min, feed rate f = 0.8mm/r is the optimum amount. The test result was used on a CA6140 lathe with V=109.8m/min, f=0.8mm/r. The outer circle of the high chromium white cast iron slag slurry valve plate was not damaged by chipping, and the durability (VB=0.1mm) reached 65 points. . The original chipping occurred when V=142m/min and f=0.2mm/r. 5 Conclusion The use of the finite element method to calculate the temperature field of the tool under the combined action of cutting temperature field and cutting force is feasible. Considering the influence of stress on the tool strength, it is economical to optimize the cutting amount of high-chromium white cast iron cutting with ceramic cutting tools to ensure the lowest cutting cost and no chipping damage.
About Silicone Door Stopper
As we know,there are many parents like to play with their children at home,and sometimes when they open the door will hit the child who is not flexible.At this time,they need a door stopper.And we have this kind of Silicone Door Stop,And you can change its design and color.Just put the Silicone Door Stopper under the door that will better.
Made of high-quality Silicone,cute shape,Durable,solid design ensures years of use.
So soft that won't scratch door,wall,floor,without scratching the floor and door surface like other metal stoppers.
This door stops will keep doors securely open,ensuring that your cat,dog,kids or baby remain safe from slamming doors.
Made from flexible silicone to easily wedge under doors without leave bad odor smells like other door stops.
There are many Silicone Door Stopper Wedge wanna recommend you such as Silicone Door Stopper for Baby,Baby Door Stopper,Door Draft Stopper.
Product introduction:
1.Product name:Silicone Door Stop,Silicone Door Stopper,Silicone Door Stopper Wedge,Silicone Door Stopper for Baby,Baby Door Stopper,Door Draft Stopper
2.Place of origin:Guangdong China
3.Color:any pantone color
4.Effect:Any effect according to customer's requirement
5.MOQ:500pcs.
6.Package:1 pcs/opp,customized design is available.
7.Design:Customized/stock
8.Certification:FDA,LFGB,SGS,ROHS,etc.
9.Usage:To prevent doors from being accidentally closed and clamped onto the baby's hand
10.Silicone Door Stopper photos for reference.
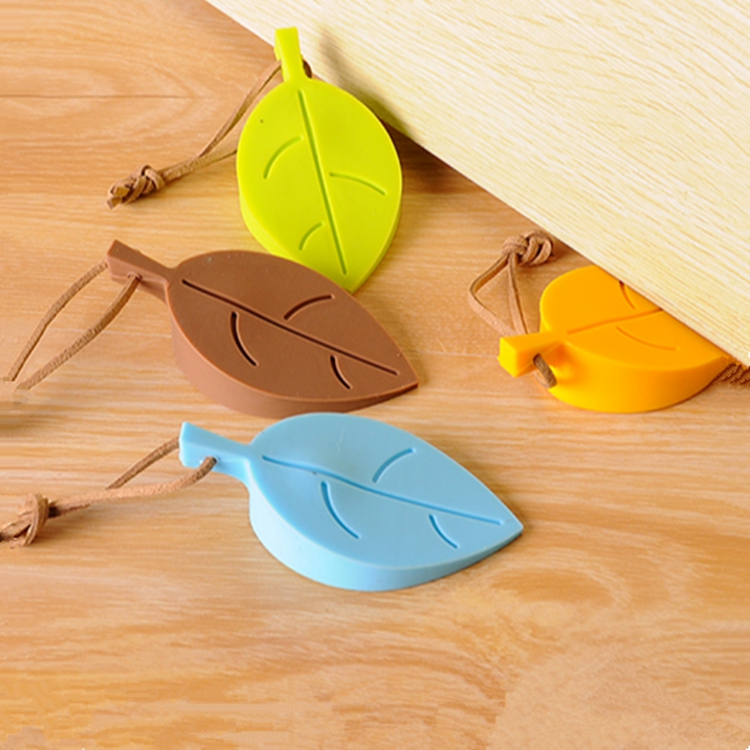
Silicone Door Stopper
Silicone Door Stop,Silicone Door Stopper,Silicone Door Stopper Wedge,Silicone Door Stopper for Baby,Baby Door Stopper,Door Draft Stopper
Dongguan OK Silicone Gift Co., Ltd. , https://www.dgsiliconebabyproducts.com