Lingbao Jinyuan Tonghui Refining Co., Ltd. is a comprehensive member of Shanghai Gold Exchange. It is designated as a standard gold ingot enterprise by Shanghai Gold Exchange. Its leading products are Au99.99, Au99.95, Ag99.99 and Ag99. .95. Since 2003 production, some raw gold electrolytic refining gold containing osmium, iridium, ruthenium, rhodium, palladium, platinum group metals, which are in the electrolysis process, enriched by the long accumulated to the anode mud, mud anode casting silver and gold refractory alloy melted to form metallic gold deposited on the bottom of the crucible graphite anode plate. Platinum group metals interfere with the normal progress of gold electrolysis, affecting the quality of finished gold. This part of the gold also caused a backlog of gold and silver in the gold electrolysis process. The traditional inorganic solvent dissolution method can not effectively recover the gold and silver in the refractory gold. Due to the long-term existence of refractory gold, a large amount of liquidity is accumulated, which affects the production and operation of enterprises.
The author researched and developed the refractory composite gold separation process, realized the separation of gold and silver and platinum group metals in refractory gold, and solved the problem of long-term backlog of gold in the gold electrorefining process due to the combination of gold. After the application of the process flow, the satisfactory separation index of gold, silver and platinum group metals was obtained, and good economic benefits were obtained.
First, refractory composite gold composition
The main components of refractory gold are gold, silver, antimony, bismuth and antimony, followed by platinum, palladium and iridium platinum group metals, and trace amounts of antimony metals such as iron , lead and copper . The main component analysis results are shown in Table 1.
Table 1 Analysis results of main components in refractory gold
element | gold | silver | iridium | ruthenium | platinum | rhodium | palladium | osmium |
w B /% | 64.51 | 7.32 | 6.33 | 4.67 | 0.23 | 0.18 | 2.45 | 5.56 |
Second, the process flow
The refractory gold containing a platinum group metal, particularly a high content of lanthanum, cerium, lanthanum and cerium, is in a dense state and is usually difficult to dissolve with an inorganic solvent. After the refractory gold is treated by the metal fragmentation method, the activator is melted at a high temperature to alloy the noble metal with the activator. After the beads and nitric acid are dissolved, silver and impurity elements are removed, and 90% of the gold in the refractory gold is extracted.
The physical properties of the platinum group metal having a high melting point and a relatively high density make it precipitate with a small amount of gold at the bottom of the crucible. The residual refractory gold is melted and activated and melted. After the alloy is splashed, the active metal and silver are dissolved by acid to convert the noble metal into a highly dispersible, highly active, readily soluble metal state, and then dissolved in gold, and filtered. The solution is reduced by sodium nitrite to recover gold; after filtration, the filter residue is a high-grade platinum group metal fine powder, and the platinum group metal in the solution is replaced by zinc wire.
The process flow is shown in Figure 1.

Figure 1 refractory gold processing process
Third, the condition test
(1) Effect of the amount of activator added on the melting rate of refractory conjugated gold
At 1100 ° C, the insoluble gold was activated by 2 to 10 times the activator of the raw materials, respectively, and the results were as shown in Table 2.
Table 2 Activator dosage test results
Raw material melting rate /% | 20 | 40 | 60 | 80 | 95 |
Activator addition | 2 | 2.5 | 3 | 3.5 | 4 |
Description: The amount of activator added is the activation dose: the amount of raw materials
It can be seen from Table 2 that when the amount of the activator is 4 times that of the raw material, the refractory gold is melted by 95%. The amount of activator was determined to be four times that of the starting material.
(2) Effect of activation melting time on melting rate of refractory conjugated gold
At 1100 ° C, 4 times the activator of the raw materials was added, and the refractory gold was melted and activated for 0.5 to 2.5 h, respectively. The test results are shown in Table 3. The results showed that the melting effect of refractory gold was not significantly different from 2.5 h after 2 h of melting activation. The activation time was determined to be 2 h.
Table 3 Activation melting time test results
Melting rate /% | 20 | 40 | 60 | 93 | 95 |
Melting activation time / h | 0.5 | 1 | 1.5 | 2 | 2.5 |
(3) Effect of the number of activations on the melting rate of refractory conjugated gold
In the actual production, it is found that the number of activated melting has a great influence on the melting of the refractory gold. At 1100 ° C, activation melting 2 h, the amount of activator 4 times the raw material, the number of activated melting times 1 to 3 times on the melting of refractory gold is shown in Table 4.
Table 4 Test results of activation melting times
Melting rate /% | 20 | 40 | 60 | 80 | 100 |
Number of activations | | | 1 | 2 | 3 |
The results in Table 4 show that after three activation meltings, the refractory gold can be completely melted.
(4) The effect of the first activation time on the gold extraction rate
During the test, it was found that different first activation melting times have a great influence on the separation of gold and refractory gold. The appropriate first activation melting time will separate most of the gold from the raw materials, which can greatly reduce the reagents for the dissolution and reduction of gold in the aqua regia, shorten the process and reduce the production cost. At 1100 ° C, 4 times of the raw material activator was added and melted for 0.5 to 2.5 hours, respectively. The effect of the separation on gold is shown in Table 5.
Table 5 First melting activation time test
Gold extraction rate /% | 20 | 40 | 80 | 90 |
Melting activation time / h | 0.5 | 1 | 1.5 | 2 |
The first activation melting time was 2h, and the gold extraction rate was 90%.
According to the process conditions, the experiment was carried out to determine the optimal operating conditions: melting temperature 1100 ° C, adding 4 times the activator of the raw material, melting 2 h; residual refractory gold repeated operation 2 times, nitric acid dissolved, washing, refractory gold It is converted into a metal powder, which is recovered by aqua regia to recover gold. The total recovery rate of gold can reach over 99.90%.
(5) Production indicators
After the process and conditions were applied to the production, good separation indexes of gold and platinum group metals were obtained. Production indicators are shown in Table 6.
Table 6 production indicators
years | Raw material quality /kg | gold | silver | Platinum group metal | Recovery rate/% |
quality /kg | Quality score /% | quality /kg | Quality score /% | quality /kg | Quality score /% | gold | silver | Platinum family metal |
2006 | 29.5 | 19.5 | 99.50 | 5.0 | 99.00 | 5.0 | 60 | 99.3 | 99.5 | 99.0 |
2007 | 32.98 | 21.48 | 99.99 | 6.0 | 99.00 | 5.5 | 65 | 99.9 | 99.5 | 99.0 |
Fourth, the conclusion
(1) In the activation and melting process, the separation rate of gold and the melting rate of refractory conjugated gold increase with the addition of the activator, the number of activations of activation, and the activation time. Among them, the activation melting time has the most obvious effect. Under the optimal conditions of melting time 2h, temperature 1100 ° C and activator addition amount of 4 times, the gold extraction rate of refractory gold is above 90%.
(2) A small amount of platinum group metal in the acid dissolution process is not lost, and can be recovered by zinc wire replacement.
(3) The gold content of high-grade platinum group metal powder is 0.05%, silver is about 10%, and the total recovery rate of gold is over 99.9%.
(4) High-grade platinum group metal powder can be activated by adding activator and dissolved in aqua regia to form platinum-containing metal noble liquid, separated and purified by extraction method, or directly sold to a professional processing plant for maximum economic benefit.
(5) The activators used in the process are safe and non-toxic, and can be purchased in various markets. This process can be used alone or in combination with precious metal electrolytic refining processes.
Waste Rubber Pyrolysis Machine could process kinds of waste rubbers,
like rubbers of sliced tyres, rubbers of old shoes, rubbers of waste rubber products etc.
the total power is 11.5kw-17.5kw each whole set machine.
the oil output will be from 40%-90% or even higher if it is pure rubbers.
the main process is that by heating the reactor directly, rubbers will be pyrolysised into oil gas;
condensers or cooling pipes will cool the gas down into liquid oil with the help of recycling water;
then the rest gas which could not be cooled down into liquid oil will be recycled into reactor heating system; after oil gas coming out completely, stop heating the reactor, and cool down reactor below 70 degrees; then can open the door and discharge carbon black automatically...
there are models with capacities from 5tons to 20tons per batch
LN-2200-6000 capacity of 5-6ton
LN-2200-6600 capacity of 7-8ton
LN-2200-8000 capacity of 9-10ton
LN-2600-6600 capacity of 10-12ton
LN-2600-8000 capacity of 12-14ton
LN-2800-6000 capacity of 10-12ton
LN-2800-6600 capacity of 12-14ton
LN-2800-8000 capacity of 15-20ton
if cut into smaller pieces, it could process more.
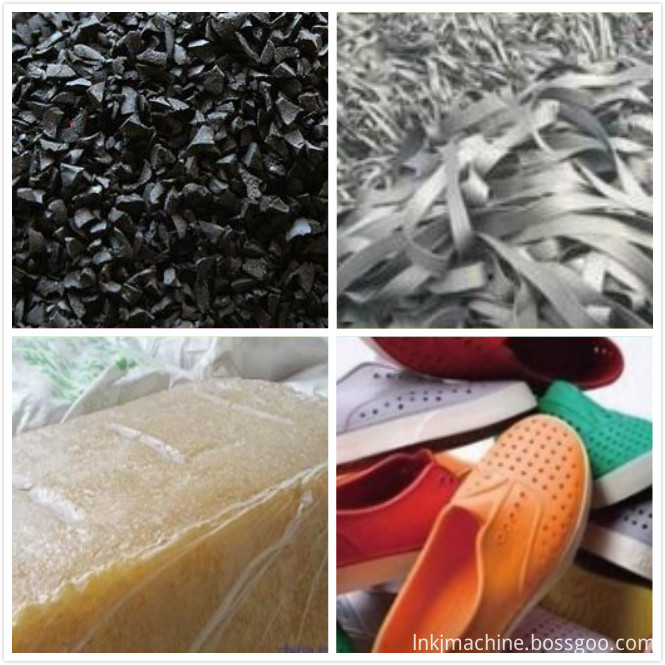
Waste Rubber Pyrolysis Machine
Waste Rubber Pyrolysis Machine,Rubber Pyrolysis Machine,Scrap Rubber Pyrolysis Machine,Automatical Rubber Pyrolysis Machine
Henan Lanning Technology Co., Ltd , https://www.lanningrecycling.com