[ China Instrument Network Instrument R&D ] Recently, researchers have developed a high-precision point access laser power meter. Its main working part is a folding mirror called a smart mirror. The use of this component enables real-time in-situ measurement. Laser power becomes possible. Unlike most conventional measuring instruments, smart mirrors are compact and fast, allowing laser power to be reported at any time during laser manufacturing without interrupting the process.
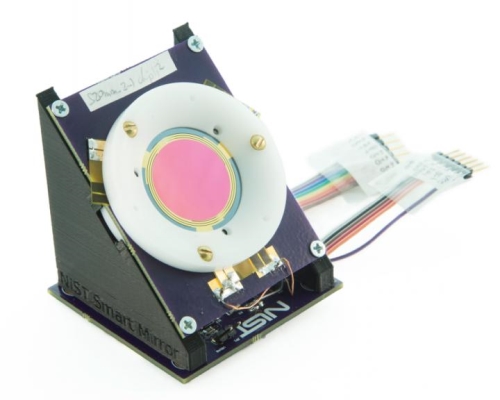
The device in the figure is the prototype of the capacitive pressure sensor of the monitoring system. The researchers designed it to measure the 1000 W laser in the infrared band. Ultimately, the error will not exceed 1%.
The power meter was designed by a team from the National Institute of Standards and Technology (NIST). They used a capacitance-based force sensor while combining the high-reflectance mirrors and sensing elements into a compact, small-cubic package. — A cube with a 4 cm side that can be embedded in a laser optical system or a laser welding system.
This smart mirror acts like a power meter that relates the effect of the laser light on the mirror to the power (ie, brightness) of the laser. At present, NIST scientists are improving these devices to embed them in laser-based processing and manufacturing tools to improve the performance and reliability of processed products.
The working principle of the smart mirror laser power meter lies in its ability to measure the radiation pressure of the laser. When a laser beam strikes an object, such as a mirror, a beam with a certain momentum will exert a small force on the mirror. This force is called the radiation pressure and it has a direct relationship with the laser power. For example, a beam of 200W power produces a force equivalent to 100 micrograms.
The researchers used a smart mirror's capacitive compact force sensor to calculate the radiation pressure. At the same time, they added a silicon spring. The silicon spring supported a circular plate with a high-reflectance mirror on one side and an electrode on the other side. Another identical spring with electrodes is placed next to the first spring so that the two electrodes face each other, forming a variable capacitor.
The laser beam reflected from the mirror on the first spring will cause the spring to move toward the second spring, which will change the capacitance between the two electrodes. To calculate the laser power, the researchers performed comparative experiments using a fixed reference capacitor. In addition, after the laser is reflected from the mirror, it can be used for work purposes. This allows the system to monitor the laser power in real time or perform laser calibration.
Researcher Alexandra B. Artusio-Glimpse said: “The manufacturer can continuously measure the laser power and monitor the laser calibration in real time during each welding process. As long as the laser has a problem, the skilled worker can know through monitoring that there will be no waste when the welding is bad. The risk of metal parts."
The early generation of this monitoring system was about the size of a shoe box, with a measurement sensitivity of 50 μg and a response time of 5 seconds. With the new generation of smart mirrors, the measurement sensitivity was improved by 100 times and the response time was reduced by 50 times. The team also successfully mitigated the static droop error caused by gravity when the device was rotated. These improvements allowed the researchers to embed the sensor in the end of the robot arm or embedded in an additive manufacturing and laser welding system where the laser head can move and rotate.
The results of preliminary tests show that the new tester is sensitive enough to measure laser power of 100 W and the uncertainty of measurement is less than 1%, and its response time is also faster than other absolute high power laser measuring instruments. Currently, researchers are continuing to test these results with more tests. According to researcher Artusio-Glimpse, the NIST team is expected to establish a new generation of smart mirror laser power meters with important standard performance in the near future.
Artusio-Glimpse also said: "Measuring the laser power by measuring the laser beam's impact on the mirror's pressure is a very unique technique. To date, it is the only true in-situ laser power measurement technology, with other optical power measurements. The biggest difference in technology is that our method allows us to continue working with lasers while measuring.â€
(Original title: Point-of-use power meter can monitor high-power lasers in real time)
Automatic electric chuck, claw DC motor drive, clamping motor current is sensitive, adjustable and stable, clamping range is wider and clamping force is larger. Non - destructive pipe clamping, fast automatic centering and clamping pipe, performance is more stable. The chuck size is smaller, rotation inertia is low, and dynamic performance is strong. Self-centering electric chuck, gear transmission mode, higher transmission efficiency, long working life and high work reliability.
Laser Tube Cutting Machines,Tube Cutting Machine,Tube Fiber Laser Cutting Machines,Tube Fiber Laser Cutting Machine
Jinan Bodor CNC Machine Co., Ltd. , https://www.bodorcnc.com